Modular Can Reduce Construction Risks
Wood construction has a myriad of benefits, but a very recent and very large construction site fire illustrates the dramatic risks of using wood as a site-built material. The project was large: five-story; 241-unit; and $51 million.
This building was, no doubt, designed to meet all fire and building codes upon completion, but, at 40% completion, the exposed wood framing was a substantial fire risk. This illustrates yet another two reasons to use off-site modular construction. First, using modular dramatically decreases on-site construction time, thereby reducing the construction risk window. Second, with very little change to design and production, the wood frame walls could be shipped already contained within fire rated assemblies.
Thinking about modular MMC construction, add these two items the “Pros” column.
Prefab: Global Affordable Housing Solutions
Speaker:
James B. Guthrie, AIA
Miletus Group, Inc.
The global need for affordable housing is massive and growing rapidly. India alone estimates that they currently have a housing shortage of over 18 million dwelling units, and that number continues to grow. China and many African nations are in a similar condition with population growth fast out pacing housing production. Skilled construction labor is in short supply.
Working with an international consortium, James B. Guthrie, AIA, president of Miletus Group, Inc., has developed designs and a design-build strategy to bring the benefits of prefabrication and modern methods of construction to worldwide areas of need.
James will share the story of the design, its design-build process, and how this international team came together to offer a new scheme for building worldwide affordable housing.
Brown Bag Roundtable: Modular Architecture
Tuesday, March 25, 2014 — 12:00 – 1:30PM
AIA San Diego Chapter Office
233 A Street, Suite 200
San Diego, CA 92101
http://www.aiasandiego.org
AIA SD – Modular Roundtable Jan 28, 2014
Open discussion January 28, 2014.
This will be an open discussion session covering all things prefab. All AIA members are welcome to join the conversation.
Brown Bag Roundtable: Modular Architecture
Tuesday, January 28, 2014, 12-1:30 pm
AIA SanDiego Chapter Office
233 A Street, Suite 200
San Diego, CA 92101
http://www.aiasandiego.org
Modern Desert Prefab
Guest Speaker: Richard Orne, Architect
AIA San Diego Modular Architecture
Brown Bag Meeting Nov 26, 2013
With a dramatic 10 acre sweeping Borrego Springs desert site, a creative approach and a kit of prefab parts, Richard Orne, Architect designed and built his own modern desert home. An example of the best of Borrego Modern design, the house uses cutting edge systems-based construction technology to build a house that is in tune with its context.
AIA members are welcome to come hear about this impressive implementation of offsite construction from the architect/client’s perspective.
Richard Orne, Architect will share his thoughts and experiences on building with a set of systems based building tools to achieve a custom work of Architecture.
AIA members are welcome to join the meeting. Lunch will be provided by the AIA.
Brown Bag Roundtable: Modular Architecture
Tuesday, November 26, 2013 — 12:00 – 1:30PM
AIA San Diego Chapter Office
233 A Street, Suite 200
San Diego, CA 92101
http://www.aiasandiego.org
Modular and Prefab Library Working Group
AIA San Diego Modular Architecture
Brown Bag Meeting Sept 24, 2013
This will be a working group session to build shared knowledge base resources regarding architecture and prefabrication. Bring information about your favorite books, magazine articles, blog posts and other references to share on the AIA’s KnowledgeNet Modular and Prefabricated Architecture Group website (http://network.aia.org).
We will upload what we can and prepare a bibliography for the rest.
Brown Bag Roundtable: Modular Architecture
Tuesday, Sept 24, 2013 — 12:00 – 1:30PM
AIA San Diego Chapter Office
233 A Street, Suite 200
San Diego, CA 92101
http://www.aiasandiego.org
High Rise Prefab: Current Trends
Presentation and Discussion
AIA San Diego Modular Architecture Group
Brown Bag Meeting May 28, 2013
The next meeting of the AIA SD Modular BBRT will focus on current trends in prefabricated modular high rise architecture. In recent years we have seen 18, 24 and now 32 story buildings being manufactured as modules offsite. James Guthrie, AIA will give a short presentation on recent tall factory-built buildings from the UK and US. After the presentation, the meeting will be open for discussion on related issues. From structural techniques to general aesthetics, AIA members are welcome to come see examples and share their thoughts.
Brown Bag Roundtable: Modular Architecture
Tuesday, May 28, 2013 — 12:00 – 1:30PM
AIA San Diego Chapter Office
233 A Street, Suite 200
San Diego, CA 92101
http://www.aiasandiego.org
PreFab: Lessons from a Local University
AIA San Diego Modular Architecture Group
Brown Bag Meeting March 26, 2013
When a San Diego medical group wanted to expand their radiation oncology center, they sought speed and quality. To meet these goals they choose prefabrication.
AIA members are welcome to come hear about this impressive implementation of offsite construction from the client’s perspective.
Mike Engel, AIA will share his experience on this project. Mike is currently the Healthcare Studio Director at avrpstudios in San Diego. Formerly, he was the project architect for the local medical group during the design and construction of this prefab project.
AIA members are welcome to join the meeting.
Brown Bag Roundtable: Modular Architecture
Tuesday, March 26, 2013 — 12:00 – 1:30PM
AIA San Diego Chapter Office
233 A Street, Suite 200, San Diego, CA 92101
http://www.aiasandiego.org
ACSA Offsite Conference in Philadelphia
Offsite Conference was Historic
The Association of Collegiate Schools of Architecture (ACSA) recently (September 27-29, 2012) concluded their fall conference Offsite: Theory and Practice of Architectural Production in Philadelphia. Miletus Group was proud to sponsor the keynote address: Offsite in the UK. It was given by Jaimie Johnston, Director at Bryden-Wood, London. Miletus President James B. Guthrie, AIA also moderated a couple of panels and attended a number of the papers given. Schools from all over the US and several other countries were represented as both presenters and attendees.
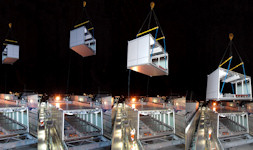
Bryden-Wood
BAA Airport Corridor Product
The depth of the research and conversation was impressive. This may be the first time so much brain power has been singularly focused on the discussion of the past, present and future of offsite and prefabricated construction methods in architecture. It gives one hope that the architectural community is embracing this method of construction with a greater depth of interest and knowledge than it ever has before. In the past we have seen some dabbling by some famous and not so famous architects, but at the ACSA conference there was a very real depth and breadth to the conversation of offsite as an architectural solution. It remains to be seen if this event will be The inflection point of offsite moving from an architectural novelty to an integrated part of the building of architecture, but it may very well be.
As Guthrie pointed out in his keynote introduction: “If we look at the long history of iron and steel in architecture, we see its roots as a non-architectural structural building material at the beginning of the 19th Century. At that time it was embraced by structural and cost engineers. 80 years later, a French bridge engineer caught the world’s imagination by building the functionless yet dramatic Eiffel Tower. About that same time Jennings and Sullivan were in Chicago developing the first architectural expressions based on iron. It took another 40 years until Mies turned it into poetry. In the historic arc of offsite construction, we are at the time of Sullivan. The coming years should prove very exciting as architects learn to use and exploit offsite.”
The papers from the ACSA fall conference on Offsite will be published soon.
For more on ACSA: http://www.acsa-arch.org
AIA SD Modular Architecture Brown Bag Meeting: September 25, 2012
Topic: Open Discussion
All AIA members are welcome to join this casual and open discussion of modular and offsite architecture. Come and share your questions and experiences on the current and future state of prefabrication in architecture.
For more information: http://www.aiasandiego.org
All AIA members and allied building professionals are welcome to join these meetings.
Brown Bag Roundtable: Modular Architecture
Tuesday, September 25, 2012 — 12:00 – 1:30PM
AIA SD Offices, 233 A Street, Suite 200, San Diego, CA 92101
Special PreFab Guest and Training at AIA SD Modular Architecture Brown Bag July 24-25
Special Guest: Researcher, Educator and Author Ryan Smith
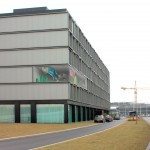
Modular Hotel Netherlands
(c) James B. Guthrie, AIA
Ryan Smith, author of PreFab Architecture (Wiley 2010) and Professor of Architecture at U of Utah, will be attending the July meeting of AIA SD’s Brown Bag Round Table discussion of modular and prefabricated architecture. This meeting will be a casual and open discussion format. Come and share your questions and experiences on the current and future state of prefabrication in architecture. Topics to include the prefabrication process in design and building, lean construction, green building, integrated technologies, global developments and more. For more information: http://www.aiasandiego.org
You are also invited to attend Prof. Smith’s more formal Offsite Design Workshop on Wednesday July 25 at the AGC training facilities in San Diego. This is a half-day morning seminar that will provide more detailed information on prefabrication in architecture and building. AIA members can earn 5 continuing education LUs. For more information: http://www.prefabeducation.com/Prefab_Education/San_Diego.html
All AIA members and allied building professionals are welcome to join these meetings.
Brown Bag Roundtable: Modular Architecture
Tuesday, Tuesday July 24, 2012 — 12:00 – 1:30PM
AIA SD Offices, 233 A Street, Suite 200, San Diego, CA
Offsite Design Workshop (5 AIA LU’s)
Wednesday July 25, 2012 — 8:00 – 12:00PM
AGC Training Facility, 6212 Ferris Square, San Diego, CA
Modularize Your Architecture at Modular Architecture Group
The next meeting of the San Diego AIA’s Modular Architecture Group will be an open discussion regarding when and how to modularize your designs. Bring one of your current projects for a roundtable discussion on its merits as a potential modular construction, and how conversion can be accomplished. Projects that make good candidates for modularization include: multi-family housing, student housing, classrooms, hotels and hospital patient wings.
All AIA members are welcome to join the meeting.
Brown Bag Roundtable: Modular Architecture
Tuesday, March 27, 2012 — 12:00 – 1:30PM
AIA San Diego Chapter Office
AIA San Diego: http://www.aiasandiego.org
Modular Architecture Q&A: Modular Shapes
Below is the next post, number 6, in the continuing series of prefab/modular Q&A asked by Norman Gray, a graduate student at the New School of Architecture and Design in San Diego, CA and answered by James B. Guthrie, AIA, President of Miletus Group, Inc.
Question:
How can prefab modules be designed so that they are not only rectangular or limited to prefabricated looks like stacked blocks?
Answer:
That is an easy one. Owners and developers who want to build prefab or modular architecture should hire an architect. There is no question that the supply chain in the US has been stuck with boring boxy forms. However, this has more to do with a lack of creative pressure than anything else. While the analogy to Lego® blocks can be fun, there is nothing that requires prefabrication of building components to be as repetitive in form as rectilinear blocks. Blocks do have some efficiencies, but they are minimal. A creative architect who understands how prefab building is done can come up with non-rectilinear forms that can be built as easily as common box forms.
Related link: http://www.newschoolarch.edu
© Miletus Group, Inc. 2012
Modular Architecture Q&A: New Materials or Technologies
Below is the next post, number 5, in the continuing series of prefab/modular Q&A asked by Norman Gray, a graduate student at the New School of Architecture and Design in San Diego, CA and answered by James B. Guthrie, AIA, President of Miletus Group, Inc.
Question:
Are there any new materials or technologies which are making prefab construction more cost effective?
Answer:
As far as I am aware, no none that directly pertain to offsite construction.
There are some new building materials on the horizon that show promise, but as of yet they have not made it into prefab production. At this time, the cost benefit of prefab is in the process, not the materials. This could easily change in the near future as the supply chain becomes more robust, but for now the focus has been on tweaking standard methods to make building more cost effective.
Manufacturing processes that allow repetitive work to be done quickly is the chief driver of prefab right now. Quick assembly once on the site is another. Use of sustainable building practices is yet another. Perhaps one aspect of using manufactured processes that is a new benefit to the building world is the idea of greater precision in building. Products produced in a factory setting are inherently built more accurately than on site work. This can translate into stronger and more efficient buildings. The application of the methodology to architecture is somewhat new. The building materials and technologies, however, still tend to parallel standard construction.
Related link: http://www.newschoolarch.edu
© Miletus Group, Inc. 2012
Modular Architecture Q&A: Population vs Construction
Below is the next post, number 4, in the continuing series of prefab/modular Q&A asked by Norman Gray, a graduate student at the New School of Architecture and Design in San Diego, CA and answered by James B. Guthrie, AIA, President of Miletus Group, Inc.
Question:
How do you think increasing populations and decreasing jobs will effect construction and what role will prefab play in this environment? World Populations: 1938 2 Billion, 2006 6.5 Billion, 2030 8.3 Billion.
Answer:
This is an interesting question. I think that if you look at China and India right now you will see two countries that are experiencing a great deal of population growth pressure. In these countries, you can already see some of the answers that occur in these kinds of resource stressing situations. Because of the prefab benefit of speed to occupancy, both China and India are becoming bigger and bigger proponents of prefab construction. They are already implementing these methods at a greater pace than most other countries. They have learned that when the complete supply chain is in place, prefabrication can be used to turn out a great deal of building square footage very fast.
While quick building does move toward ‘solving’ the problem of housing shortages, it is typically being done with generic buildings, not architecture. Unfortunately, just creating housing rapidly means there will be a lack of consideration for how people live and how that housing works within a cultural context. This will naturally lead to significant social problems down the road. This is, though, not a problem caused by prefabrication, but prefab may wind up taking the blame. The problem, at its root, is caused by societies reacting to the past and not planning or designing for the future. This is one reason I am such an advocate for architects becoming more knowledgeable about prefabrication. If architects do not, good design will be ignored for speed. In the end, nothing good will come from that.
Where is the architecture?
– Video of 15 story Chinese hotel built in 6 days:
http://youtu.be/JtdorKaOSQk
– Video of 30 story Chinese hotel built in 15 days:
http://gizmodo.com/5873962/amazing-timelapse-of-30+story-building-made-in-only-360-hours
Related link: http://www.newschoolarch.edu
© Miletus Group, Inc. 2012
Modular Architecture Q&A: Project Size vs Economics
Below is the next post, number 3, in the continuing series of prefab/modular Q&A asked by Norman Gray, a graduate student at the New School of Architecture and Design in San Diego, CA and answered by James B. Guthrie, AIA, President of Miletus Group, Inc.
Question:
Is there a minimum size for a project to make prefab economically viable?
Answer:
No. Prefab is a generic concept that has been used to make buildings as small as garden sheds (1 small module) and as large as a 24 story apartment building (500+ large modules). Viability is determined by all the factors that go into making the building, including understanding the supply chain that produces the factory made components and the efficiencies inherent in that chain.
In the case of the garden shed, the sheds are standard designs produced by the hundreds, if not thousands. In the case of the 24 story building, the resulting building is a single architectural structure. One commonality that lead to the economic success in both examples is the use of repetition where repetition made sense. In the case of the garden shed, repetition is probably obvious as each shed is a copy of a singular design. In the example of the 25 story building, the architect cleverly exploited repetition in the layout of the apartments so that very few unique modules were used yet an overall creative architectural solution was achieved.
The fundamental lesson of economic viability here is that if you want to use prefab for a small building, make many replicas of the same building. If you want to use prefab for a large building, make it from many similar components.
Related link: http://www.newschoolarch.edu
© Miletus Group, Inc. 2011
Modular Architecture Q&A: Transportation Costs
Below is the second post in the continuing series of prefab/modular Q&A asked by Norman Gray, a graduate student at the New School of Architecture and Design in San Diego, CA and answered by James B. Guthrie, AIA, President of Miletus Group, Inc.
Question:
Is transportation of prefab/modular units a significant cost factor?
Answer:
The general answer would be ‘yes’, but how significant is dependent on the details of the project. These details include: the distance and travel conditions between the project and the factory, the size and weight of the prefab components, and the cost of labor at the two locations. To illustrate the extremes, I am aware of projects that were as simple as lightweight bathrooms pods built less than a mile from the project site, to very heavy fully furnished apartment modules that were shipped hundreds of miles, over both seas and roads, and even between two countries. The cost of the transportation was clearly very different being much greater in the second example, yet both projects made financial sense.
To understand the impacts of transportation, keep in mind that costs associated with transportation are not new or exclusive to prefab vs site built. All building construction has transportation costs inherent in the project. Regardless of the method of construction, both materials and labor come from somewhere other than the construction site.
To understand the differences, however, let’s first consider the case of the transportation of labor. In this regard, offsite construction is particularly efficient vs onsite. Workers at a factory tend to live near the factory and so have very consistent and minimal travel distances to the work site (ie the factory). Additionally, carpooling and other energy efficient commuting options become very real in this scheme. In the case of onsite construction, the travel distance for labor is a variable and completely dependent on the location of the trades needed and the building being constructed. Onsite construction requires a more skilled labor force than offsite construction. It is often the case the specialty trades will travel greater distances to reach a construction site than unskilled labor to factories. For onsite construction the location of the worker to the work site is in constant flux with each building built. This is not so with offsite methods.
There is a similar effect with the delivery of materials. Offsite construction occurs on singular factory sites where there tends to be large and protected staging areas. This means materials can be ordered and stored in weather protected areas in bulk far in advance of assembly. Factories also tend to be geographically clustered and located within proximities to construction material suppliers. These two factors greatly increase the efficiency of material delivery to the point of assembly.
For prefab, there is then unique cost of transporting large assemblies to the building site. Unlike traditional onsite labor and material logistics, however, prefab assemblies carry with them substantial embodied bulk material and embodied bulk labor, and are thus extremely efficient transportation hauls.
Because of these efficiencies and the addition of labor to the total transportation cost of building, the equation of transportation related costs and its percentage of the total building cost, has many components and modifiers to consider in the final equation. This is why, depending on the project, it can actually be cost effective to ship large and heavy modules long distances.
Related link: http://www.newschoolarch.edu
© Miletus Group, Inc. 2011
Modular Architecture Group
AIA Meeting Dec 6, 2011 in San Diego
Q: What do the Marmol-Radziner Desert House, the Sunset Breeze House, the WIRED Livinghome and High Tech High all have in common?
A: They are all modular and they were all engineered by the modular experts RS Tavares Associates!
Come hear Ralph Tavares, PE share his insights into these and other special modular buildings at the next Brown Bag Roundtable on Modular Architecture.
All AIA members welcome. For more information, link here.
Brown Bag Roundtable: Modular Architecture
December 6, 2011
12-130pm
San Diego AIA
If you are unable to attend this meeting, consider joining the The Modular and Prefabricated Architecture Group on the AIAKnowledgeNet.
© Miletus Group, Inc. 2011
Modular Architecture Q&A: Time and Money
James B. Guthrie, AIA, the President of Miletus Group, Inc, was recently approached by Norman Gray, a graduate student at the New School of Architecture and Design in San Diego, CA regarding an architectural project he was working on. As a part of his research, Mr. Gray sought our expertise in answering several questions regarding prefab and modular construction. We thought the questions were very good ones and worth sharing with a wider audience. We will post each question and answer as a separate blog post. Readers who have their own questions about modular architecture are encouraged to ask us as well.
Question:
What percentage of time and money do you think prefab can save a project?
Answer:
When it comes to prefab, generalized questions can be difficult to answer. In general, on a direct apples-to-apples comparison, I would say that you could expect that a prefab project can be 0-15% less per square foot than a traditionally built project of the same design and specifications. There are too many variables, though, to allow a hard and fast rule as to discounts.
It is also important to keep in mind that when we are talking about prefab, we can be talking about prefab architecture or prefab building. When I talk about prefab architecture, I am using the idea that architecture is a high quality building designed by a professional and it is always site specific. This means that each prefab architecture project will be unique to the site it is being placed on. The quality of the end result will be high quality, and the owner will be a ‘client’ of a professional architect. Prefab building, in contrast, is a generic ‘product’ that can be non-site specific. The quality can vary dramatically from project to project and the owner of this product is a customer of a building company.
The other important thing to consider is the definition of “project”. Architects tend to think of a project as the specific building they are working on. Building owners, however, think of a “project” as the entire business model related to that building. This includes the architecture plus: land acquisition and development, operations and maintenance, financing, cash flow and other business considerations. To answer the question about prefab architecture from the architect’s side, at this time a prefab architecture project has no inherent time or money advantages to the architect except as it may add value for their clients. To answer the question from the owner’s perspective regarding prefab architecture, it can have significant time savings, which to the owner can translate into a huge financial savings to the non-architectural aspects of the project. The amount of savings is, of course, dependent on the project.
Typical Modular Home, USA
2 Offsite Stories, 1 Single Family House, 4 Modules
On the small scale, in the US right now it is very easy for a homebuyer to buy a house much like they buy a car. The homebuyer can go to a sales lot of a manufactured home builder, tour model homes, pick out their model, pick out colors and finishes, and have their new home delivered in a very short amount of time. These homebuyers are buying a prefab building, not prefab architecture. The opportunity for this kind of building to become architecture is very limited. Because prefabrication is a method of construction that takes advantage of manufacturing processes, the economic side of prefab is most successful when there is volume on the production side. One single family home does not afford current manufacturing processes the kind of efficiencies needed to be cost effective. In the case of a home or small commercial building, volume is achieved when many of the same design are produced. In this situation, the efficiency is dispersed among many buyers. This means, naturally, that each individual buyer looses the opportunity to influence the design and quality of their purchase.
Modular Housing, England
10 Offsite Stories, 162 Apartments, 630 Modules
On the large scale, the prefab building buyer is also buying the convenience of speed to occupancy, but the larger scale can allow the project to be more architectural. Fundamentally the building process is relatively the same between prefab and onsite construction, except that the offsite components can be built simultaneously with much of the onsite work. The onsite assembly of the offsite components can then occur very rapidly. On a large project this can save a lot of time, and thus a lot of money to the owner. This is important, as even if the square footage costs of onsite and offsite construction are nearly identical, the cost savings to the owner can be very significant and far exceed the 0-15% savings in square footage costs. Unlike a single family home, the size of a large project can allow the design to take on far more significant role than is possible in small projects. It is the large projects that create the greatest opportunity for all the benefits of prefabrication and the application of real architecture to meld. This is the future of prefabrication in architecture.
Related link: http://www.newschoolarch.edu
© Miletus Group, Inc. 2011
Modern Construction Lexicon – Update
Acronyms are terms made up of the initial components of words within a phrase. Eventually, acronyms become words themselves through popular use. For instance, LEED® stands for “Leadership in Energy and Environmental Design,” however most design trade professionals understand that it is an internationally recognized green building certification system developed by the U.S. Green Building Council or (USGBC). This week we have added two new acronyms, LEED and BIM, to our lexicon. The two terms are frequently referenced in Modern Methods of Construction or (MMC).
Link below to view the glossary page, which will be updated frequently with new words. We would also like to invite you to suggest new terms or expressions you would like to see added to our lexicon by typing within our comment area.
LEED® (Leadership in Energy and Environmental Design)
LEED is an internationally recognized green building certification system. It provides third-party substantiation that a building or community was designed and built to be sustainable by establishing metrics for energy savings, water efficiency, CO2 emissions reduction, improved indoor environmental quality, and stewardship of resources and sensitivity to their impacts. Founded by the U.S. Green Building Council (USGBC), LEED is an open process that is publicly reviewed and provides a framework for identifying and implementing measurable and practical green building solutions.
Miletus Group is a member of USGBC and endorses the LEED program as a powerful tool to bringing the built environment to higher levels of sustainability.
BIM (Building Information Model/Modeling)
The National Building Information Model Standard Project Committee defines BIM as: a digital representation of physical and functional characteristics of a facility. A BIM is a shared knowledge resource for information about a facility forming a reliable basis for decisions during its lifecycle: defined as existing from earliest conception to demolition. According to Building Design + Construction magazine, more than 100 top design firms identify revenue from BIM projects and in the top 10, BIM is used in 58-85% of projects. Practically, BIM is about information management, which is shared by all project participants, using technology to advance creativity, productivity, and team empowerment.
Miletus Group utilizes BIM in its workflow and believes it is a superior way to bring greater design, documentation and construction efficiencies to the architectural and modular building process.
Renovated Reuse (in modular buildings)
Renovated Reuse can be defined as a reconfiguration of an existing modular building or modular building component to meet the needs of a new configuration, use or location. Renovated Reuse can be applied to all modular buildings whether temporary or permanent. Renovated Reuse is a very green process in that whole buildings and large building components can be diverted from the landfill. In the case of reuse of modular buildings and modular components, the green process is still further enhanced, as direct reuse requires far less embodied energy than recycling. Because of their component nature, modular building components can be designed in advance, as a part of their life cycle, to be deconstructed and reconstructed so that Renovated Reuse is a strategic part of a new building’s business model.
In 2009 a Miletus Group renovated reuse modular project won an MBI Award of Distinction for its design conversion of a modular office building to a sustainable modular climate controlled warehouse.
Net-Zero Energy
Net-Zero describes buildings with zero net energy consumption from non-renewable resources and zero carbon emissions annually. Zero energy buildings do not need to be reliant on a traditional energy grid supply. Energy can be harvested using Solar, Wind or Geothermal technologies while also reducing the overall energy consumption. The zero-energy design principle is becoming more practical to adopt due the rising costs and negative impact of fossil fuels as well as the advent of efficient alternative energy sources. There is some debate in the design community as to whether or not renewable energy sources must occur on site to be considered true net zero. At Miletus Group we believe that it is more efficient to have the energy source as near to the point of use as possible, but it is not always the case that the best solution has the energy source on site. The location of renewable energy sources should be made on a case-by-case basis.
© Miletus Group, Inc. 2011
Architectural Blogs of Note – Update
We return to our feature, “Architectural Blogs of Note.” If you have an architectural blog you feel is noteworthy – please feel free to share the link by adding it to the comments area below. These blogs are selected for their quality and contribution to the online architectural knowledge base. As architects and bloggers we have a responsibility to continuously evolve our profession through smart and vibrant discussions, education, and involvement. We hope you enjoy our blog selections.
A456
http://www.aggregat456.com/search/label/architecture
A456 offers postings about architecture and design-based ideas across a variety of disciplines. Author Enrique Ramirez is a PhD candidate at the Princeton University School of Architecture, and is a 2007 graduate of the Master of Environmental Design program at the Yale School of Architecture.
Urban Planning Blog
http://urbanplanningblog.com
Pratik Mhatre (Ph.D. in Urban and Regional Science, Masters Degree in Public Policy and an undergraduate degree in Architecture) provides his thoughts on urban planning and design. He is deeply interested in the relationship of public policy and the built environment; especially the intersection of public health policies and their impact on socio-economic characteristics of the neighborhood/community.
DigitalUrban.org
http://www.digitalurban.org
Dr Andrew Hudson-Smith, author of the Digital Urban Blog with 5200 daily readers, has been at the forefront of developing digital geographical technologies that support design professionals working in the built environment. He is the Director and Deputy Chair of CASA, Editor-in-Chief of Future Internet Journal, an elected Fellow of the Royal Society of Arts and Course Founder and Director of the MRes in Advanced Spatial Analysis and Visualization at University College London.
Modular Architecture Brown Bag Group
AIA Meeting Oct 4, 2011 in San Diego
The recent growth of modular and prefabricated construction in the U.S. and abroad likely means this method of construction is reaching a tipping point in realization. If you are in the San Diego area, you are invited to a free roundtable led by Jim Wallace of American Modular. American Modular is a California manufacturer of commercial, institutional and modular buildings. For more information, link here.
Modular Brown-Bag Roundtable
October 4, 2011
12:00 pm – 1:30 pm
AIA San Diego
233 A Street, #200
San Diego, CA 92101
Phone: (619) 232-0109
Email: info@aiasandiego.org
For those outside the San Diego area, the National AIA, on the new AIAKnowledgeNet, has established The Modular and Prefabricated Architecture Group to provide a central location where architects and allied professionals can share, learn, and push the state of the art of off-site construction to new architectural levels.
© Miletus Group, Inc. 2011
Modern Construction Lexicon
Words are powerful conveyors of information – but only if we are all on the same page as far as what the words we use actually mean. And words can change in their meaning over time. Look at the phrase “pre-fab” for example. Pre-fab comes from prefabricated. This word can be applied to just about everything made these days (except most buildings). In the context of buildings it has roots in home building, as in “Prefabricated Homes.” This phrase was first used a few decades ago and commonly referred to mobile homes. To many people this reference invokes connotations of cookie cutter shapes and cheap construction methods. More recently “prefabricated” has been shortened to “pre-fab” and its meaning also has shifted to be applied to a new breed of house that is cleverly designed, manufactured, sustainable, of modern style, and of high quality. We hope our new glossary helps to clarify the meaning of words that are defining Modern Methods of Construction today.
Link below to see the new glossary page! We will update this frequently with new words. Please feel free to add new words you would like to see in the glossary in our comment area.
© Miletus Group, Inc. 2011
Modular Architecture Brown-Bag Roundtable
AIA Meeting August 2, 2011 in San Diego
Find out more about the latest methods in modern, modular construction. It’s not just theory; it’s winning prestigious design awards for architects interested in sustainable building, cost efficiency and quality control.
Come to the next meeting of the Modular Architecture Brown Bag group to hear Eric Naslund, FAIA of Studio E Architects discuss his project: High Tech High. Eric will be sharing his experiences using modular construction in his COTE award-winning design.
Modular Brown-Bag Roundtable
August 2, 2011
12:00 pm – 1:30 pm
AIA San Diego
233 A Street, #200
San Diego, CA 92101
Phone: (619) 232-0109
Email: info@aiasandiego.org
Increasing interest and the recent growth in the US and abroad of new construction substantial modular buildings, and the industries surrounding it, signifies a significant change on the architectural landscape. At the National AIA level, on the new AIAKnowledgeNet, The Modular and Prefabricated Architecture Group has been established to provide a central location where architects and allied professionals can share, learn and promote state-of-the-art offsite construction to new architectural levels.
AIA San Diego invites you to join your peers who share your interest in this topic at a local Brown-Bag Roundtable. No RSVP is necessary. This is a free, member-only, bring-your-own-brown-bag event. Food vendors are available in the building for those wishing to purchase their lunch.
High Tech High
Jim Brady Architectural Photography
High Tech High Modules
© Miletus Group, Inc. 2011
Miletus Group Returns to its Roots! Opens Chicago Architectural Office
Miletus Group has officially announced the opening of its new office in Chicago, IL at 2823 N. Milwaukee Avenue, Suite E, (312) 265-6447. The new Chicago metropolitan location will house architectural services, building on the continued success of the Miletus Group management, design, and production operations in its Rochester, IN headquarters.
“The new design office gives us a great new platform to reach out to the entire Chicago metropolitan market,” says James B. Guthrie, AIA, president of Miletus Group, adding, “We have exciting plans for innovative, large-scale modular solutions involving hotel, apartment, and healthcare facility projects,” he further explains. “Chicago is a natural market for substantial building in these sectors, making it a perfect fit for our future growth strategy. In addition, Chicago is my hometown, so I very much look forward to working there with our staff of talented architects.”
Chicago was selected as a key growth market, according to Guthrie, because of its proximity to the company’s production facility in Indiana, and because it provides a large market area with a history of progressive thinking in terms of architecture and building. Guthrie points out that early in the twentieth century, Chicago-founded Sears, Roebuck and Co. sold over 70,000 precut and prepackaged homes through their mail order Modern Homes program, which allowed customers to choose a house to suit their individual tastes and budgets. At approximately the same time, he goes on to explain, Frank Lloyd Wright introduced his textile block Usonian home concept to demonstrate that exceptional quality and design, using prefabricated components, can be made available to the masses.
“Conceptually, we stand on the shoulders of such Chicago icons as Sears and Frank Lloyd Wright, who paved the way for modular architecture,” Guthrie states. “Today, we are seeing a resurgence in modular architecture,” he continues. “The interest is driven in small part by economics, but more so by a desire for greener construction practices, creative design, and the caliber of high quality production that Miletus Group consistently delivers and will now extend into the Chicago market.”
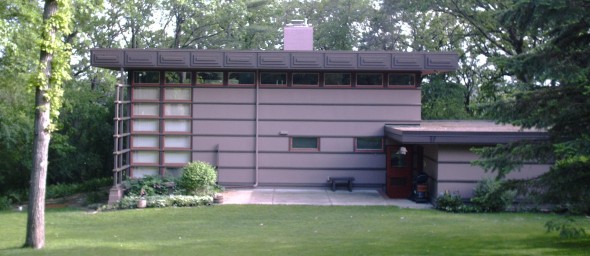
Frank Lloyd Wright McBean House in Rochester, Minnesota. This Usonian house is an example of the second type (Prefab #2) of the Marshall Erdman Prefab Houses.
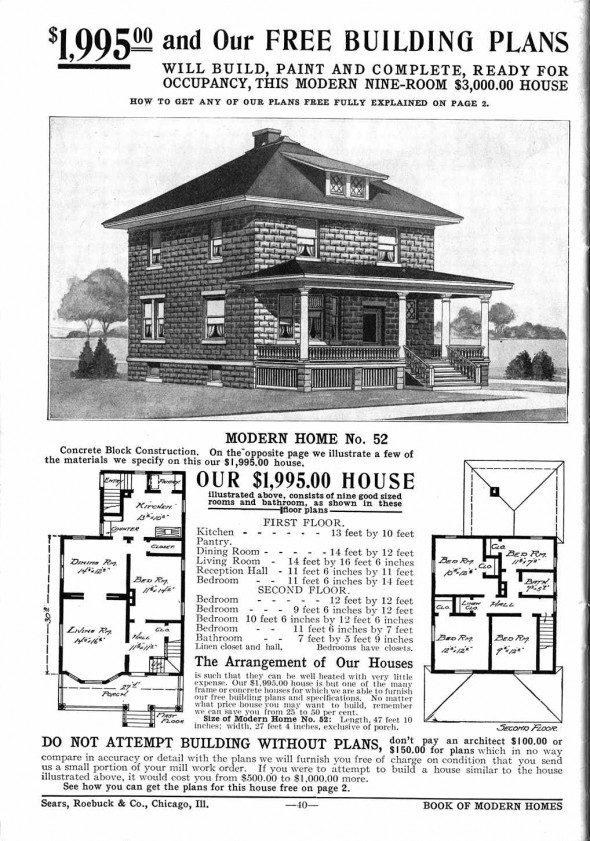
Sears Homes 1908 – 1914, Chicago, IL From the Sears Archives Model No. 52