Prefab: Global Affordable Housing Solutions
Speaker:
James B. Guthrie, AIA
Miletus Group, Inc.
The global need for affordable housing is massive and growing rapidly. India alone estimates that they currently have a housing shortage of over 18 million dwelling units, and that number continues to grow. China and many African nations are in a similar condition with population growth fast out pacing housing production. Skilled construction labor is in short supply.
Working with an international consortium, James B. Guthrie, AIA, president of Miletus Group, Inc., has developed designs and a design-build strategy to bring the benefits of prefabrication and modern methods of construction to worldwide areas of need.
James will share the story of the design, its design-build process, and how this international team came together to offer a new scheme for building worldwide affordable housing.
Brown Bag Roundtable: Modular Architecture
Tuesday, March 25, 2014 — 12:00 – 1:30PM
AIA San Diego Chapter Office
233 A Street, Suite 200
San Diego, CA 92101
http://www.aiasandiego.org
India: Demand for Housing Stresses Nation
BuildOffsite Delegation Answers the Call
BuildOffsite (www.buildoffsite.com), the leading global organization of allied professionals for modern methods of construction, was recently asked to visit India on a knowledge sharing expedition. The reason for the trip was to meet with academic, industry and government leaders to assist in finding solutions to the challenge of housing the world’s second largest and fast growing population.
James B. Guthrie, AIA, President of Miletus Group, Inc. was asked to join the small and prestigious problem solving delegation which also included allied professionals from India, New Zealand and Great Britain.
Pressure is Building
India is challenged by both the current size of its population, now over 1.2 billon, and its substantial projected population growth. 65% of India’s population is under 35 years old. While China is currently the largest country in terms of population, India is a close second and growing at a faster pace than China. Projections indicate that India’s population will surpass China by 2030. In addition to the overall growth of the population, the country is also rapidly changing from rural to urban based. While India is already the densest country in the world, currently only 31% of the population live in urban areas. As this shift continues there will be greater and greater pressure on building and supporting infrastructure in urban areas. Massive amounts of green field sites are being consumed to accommodate expanding urban lands.
Current estimates indicate that India has an existing housing shortage of over 18 million dwelling units at every income level. With the upcoming population growth and urban migration, this number is expected to become even more staggering over the coming years. India is in the midst of a very real housing and building crisis of unimaginable proportions and stands in a unique place in the world.
Population and Growth Rates 2012 – Three Largest Countries
Country | Population | Growth Rate | Annual Growth |
USA | 313,847,465 | 0.9% | 2,900,000 |
India | 1,205,073,612 | 1.3% | 15,700,000 |
China | 1,343,239,923 | 0.5% | 6,700,000 |
What this all means is that India needs a lot of new buildings and they need them quickly. Along with homes, other buildings like schools, hospitals, police stations, and stores are also needed to support the growing population. This huge demand has been creating substantial pressure on the existing construction supply chain, which still uses fairly traditional building methods. As a result, there is simply not enough skilled labor or production facilities to keep up with the demand.
BuildOffsite Called to Help
Fortunately, India’s leaders understand the dilemma and are seeking solutions to it. Thanks to forward thinkers and organizations like BuildOffsite, word has been spreading around the world that offsite methods of construction can deliver buildings more efficiently and of greater quality than traditional building methods. India sees prefabrication as a major way forward in their construction industry. Miletus Group was there to join in the solution based conversations and to promote the idea of not just fast building, but quality building including achieving social, architectural and sustainability goals.
While rapid population growth can tend to focus discussions on expediency, cost and logistics, this can spell social disaster if cultural history and social norms are forgotten in the process. India, especially, has a long and impressive cultural tradition of building magnificent buildings, most notably displayed in the elegant Taj Mahal. Over 350 years old, the Taj Mahal is as beautiful now as the day it was completed. This is due to the obsession with quality that its builders had, and is a good lesson that should not be forgotten in today’s climate of need. Architecture feeds the soul of a nation and provides future inspiration through generations of thoughtful predecessors. Factory made ‘ticky-tacky little boxes’ may provide a temporary fix, but good design, no matter how humble, will add permanency and pride to an enduring built environment. Architects must be a part of the solution and the transformation from traditional to modern methods of construction.
The Future is Now
India is a place of action. Changes to the building industry are occurring right now. Prefabricated techniques are being used in the way of precast concrete buildings. The systems are however, still a bit rough and rely on traditional onsite skills used in an offsite location. Coming soon, though are more modern offsite factories and methods that use lighter and faster framing and more sustainable building practices.
The positive energy expressed by the Indian hosts of the BuildOffsite delegation was palatable. They are ready to implement big ideas at big scales. It is not too big a stretch to imagine India, in just a few years, as the world leader in offsite construction. Miletus Group is proud and excited to have been a part of these early talks. We also look forward to being a part of the growth that is India’s present and future life.
* Demographic information from various governmental websites.
Modular Architecture Q&A: Population vs Construction
Below is the next post, number 4, in the continuing series of prefab/modular Q&A asked by Norman Gray, a graduate student at the New School of Architecture and Design in San Diego, CA and answered by James B. Guthrie, AIA, President of Miletus Group, Inc.
Question:
How do you think increasing populations and decreasing jobs will effect construction and what role will prefab play in this environment? World Populations: 1938 2 Billion, 2006 6.5 Billion, 2030 8.3 Billion.
Answer:
This is an interesting question. I think that if you look at China and India right now you will see two countries that are experiencing a great deal of population growth pressure. In these countries, you can already see some of the answers that occur in these kinds of resource stressing situations. Because of the prefab benefit of speed to occupancy, both China and India are becoming bigger and bigger proponents of prefab construction. They are already implementing these methods at a greater pace than most other countries. They have learned that when the complete supply chain is in place, prefabrication can be used to turn out a great deal of building square footage very fast.
While quick building does move toward ‘solving’ the problem of housing shortages, it is typically being done with generic buildings, not architecture. Unfortunately, just creating housing rapidly means there will be a lack of consideration for how people live and how that housing works within a cultural context. This will naturally lead to significant social problems down the road. This is, though, not a problem caused by prefabrication, but prefab may wind up taking the blame. The problem, at its root, is caused by societies reacting to the past and not planning or designing for the future. This is one reason I am such an advocate for architects becoming more knowledgeable about prefabrication. If architects do not, good design will be ignored for speed. In the end, nothing good will come from that.
Where is the architecture?
– Video of 15 story Chinese hotel built in 6 days:
http://youtu.be/JtdorKaOSQk
– Video of 30 story Chinese hotel built in 15 days:
http://gizmodo.com/5873962/amazing-timelapse-of-30+story-building-made-in-only-360-hours
Related link: http://www.newschoolarch.edu
© Miletus Group, Inc. 2012
Modular Architecture Q&A: Project Size vs Economics
Below is the next post, number 3, in the continuing series of prefab/modular Q&A asked by Norman Gray, a graduate student at the New School of Architecture and Design in San Diego, CA and answered by James B. Guthrie, AIA, President of Miletus Group, Inc.
Question:
Is there a minimum size for a project to make prefab economically viable?
Answer:
No. Prefab is a generic concept that has been used to make buildings as small as garden sheds (1 small module) and as large as a 24 story apartment building (500+ large modules). Viability is determined by all the factors that go into making the building, including understanding the supply chain that produces the factory made components and the efficiencies inherent in that chain.
In the case of the garden shed, the sheds are standard designs produced by the hundreds, if not thousands. In the case of the 24 story building, the resulting building is a single architectural structure. One commonality that lead to the economic success in both examples is the use of repetition where repetition made sense. In the case of the garden shed, repetition is probably obvious as each shed is a copy of a singular design. In the example of the 25 story building, the architect cleverly exploited repetition in the layout of the apartments so that very few unique modules were used yet an overall creative architectural solution was achieved.
The fundamental lesson of economic viability here is that if you want to use prefab for a small building, make many replicas of the same building. If you want to use prefab for a large building, make it from many similar components.
Related link: http://www.newschoolarch.edu
© Miletus Group, Inc. 2011
Architectural Blogs of Note – Update
We return to our feature, “Architectural Blogs of Note.” If you have an architectural blog you feel is noteworthy – please feel free to share the link by adding it to the comments area below. These blogs are selected for their quality and contribution to the online architectural knowledge base. As architects and bloggers we have a responsibility to continuously evolve our profession through smart and vibrant discussions, education, and involvement. We hope you enjoy our blog selections.
A456
http://www.aggregat456.com/search/label/architecture
A456 offers postings about architecture and design-based ideas across a variety of disciplines. Author Enrique Ramirez is a PhD candidate at the Princeton University School of Architecture, and is a 2007 graduate of the Master of Environmental Design program at the Yale School of Architecture.
Urban Planning Blog
http://urbanplanningblog.com
Pratik Mhatre (Ph.D. in Urban and Regional Science, Masters Degree in Public Policy and an undergraduate degree in Architecture) provides his thoughts on urban planning and design. He is deeply interested in the relationship of public policy and the built environment; especially the intersection of public health policies and their impact on socio-economic characteristics of the neighborhood/community.
DigitalUrban.org
http://www.digitalurban.org
Dr Andrew Hudson-Smith, author of the Digital Urban Blog with 5200 daily readers, has been at the forefront of developing digital geographical technologies that support design professionals working in the built environment. He is the Director and Deputy Chair of CASA, Editor-in-Chief of Future Internet Journal, an elected Fellow of the Royal Society of Arts and Course Founder and Director of the MRes in Advanced Spatial Analysis and Visualization at University College London.
Architectural Blogs of Note
New to our blog this week is a feature that we will return to on a regular basis called, “Architectural Blogs of Note.” If you have an architectural blog you feel is noteworthy – please feel free to share the link by adding it to the comments area below. These blogs are selected for their quality and contribution to the online architectural knowledge base. As architects and bloggers we have a responsibility to continuously evolve our profession through smart and vibrant discussions, education, and involvement. We hope you enjoy our blog selections.
ARCHITECTURE BUZZ!!
http://www.architecture-buzz.com/
ARCHITECTURE BUZZ offers select architecture works from around the globe. Tanakorn Koomrampai, CEO of Ergo Architect in Thailand is Managing Editor of the site and provides detailed photography, facts, and thoughtful overviews of architectural sites, award winning designs, and technology.
iModernHome
http://www.imodernhome.com/
iModernHome features beautiful photography of contemporary homes, furniture, toys, and more. The site is clean and easy to navigate with succinct overviews of the featured designs.
+Mood
http://www.plusmood.com/
+Mood is an online resource for all things relating to contemporary architecture and design. The site reviews a wide variety of projects and products well organized by category and industry served.
inhabitat
http://inhabitat.com/architecture/
Inhabitat.com is devoted to the future of design, tracking the innovations in technology, practices, and materials that are pushing architecture and home design towards a smarter and more sustainable future. Founded by NYC designer Jill Fehrenbacher as a forum for investigating emerging trends in product, interior, and architectural design.
BLDG BLOG
http://bldgblog.blogspot.com/
BLDG BLOG is devoted to “architectural conjecture, urban speculation, and landscape futures.” Essayist Geoff Manaugh explores design, art, and culture with an intellectual edge.
© Miletus Group, Inc. 2011
Finland: Tekla, Peikko and Integrated Building Teams
Finland building professionals are on the leading edge in advancing integrated building processes and teams.
The Finnish software company Tekla is pushing the limits on their BIM (building information modeling) software. Tekla’s software was originally intended for engineers so that they could improve their structural analysis, but as it developed it became a full-fledged BIM. Today contractors are also using it with the objective of planning and implementing efficient building processes. In Finland, though, they have taken yet another big step in bringing BIM into the complete integrated building process, which now includes the building materials supply chain.
James Guthrie, President of Miletus Group, Inc., was recently invited to Finland by BuildOffSite (UK) and Tekla to attend a series of seminars and field trips focusing on BIM and offsite construction there. The seminars were designed to show the state of the art in moving from BIM to BIM + Management (BIMM) and BIMM + Production (BIMMP). Tekla has been working closely with some of Finland’s principle engineers, contractors and the building material suppliers to advance greater accuracy and quality in construction through integrated approaches in design, engineering, building product development, on site construction and, soon to come, subsequent facility management.
Neither Tekla’s software nor the Finnish building teams have reached that full ideal yet, but the advances witnessed are impressive and very hopeful. The days of full implementation are not very far away.
Many architects and contractors are becoming familiar with the usefulness of BIM for providing sophisticated pre-building design and analysis, which leads to a more efficient and error free construction process. That, however, is just the beginning of where modern methods of construction are going.
During the seminars and tours, Finnish building teams demonstrated how they are integrating the total building process. Of particular note was the principle structural supplier Peikko. Peikko is supplying all of the vertical and horizontal structural components of a new 300,000 square foot shopping center now being built in Lahti, Finland.
Piekko has developed a clever integrated (steel & concrete) construction system that allows for a high degree of consistency in cross section sizing, and thus simple design consideration for length with a wide variant in strength capacity. Working with Tekla, they have also developed modeling components for the BIM environment. This means that they have essentially developed a building structural system that is virtually and actually prefabricated and componentized. This system ties the entire building process together, from first design idea through to construction. Using their system, the Tekla BIM model is easy to apply, production and construction are fast and accurate, and the end result quality is very high.
The progress being made in Finland is the promise of future efficiencies in modular and other prefabricated building systems. When a designer has flexible building systems built into their processes, and can be assured that the final building outcome will be as designed and of a high quality, prefabrication will truly become a critical part of the architectural tool kit. After generations of inefficient site built methods, this new comprehensive offsite thinking and full team integration is huge.
Related links:
BuildOffSite: www.buildoffsite.com
Tekla: www.tekla.com
Peikko: www.peikko.com
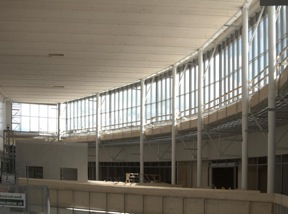
Lahti Shopping Center Under Construction
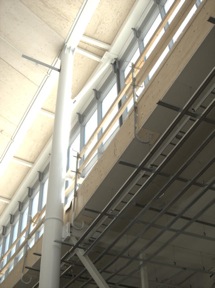
Peikko Detail
© Miletus Group, Inc. 2011
Pushing the limits of modular design.
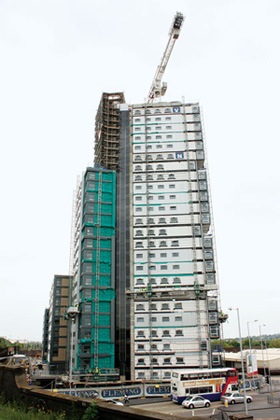
© James B. Guthrie, AIA 2011
At 25 stories, Victoria Hall, in Wolverhampton, England, is the world’s tallest building built with off-site construction methods.
Built as an apartment complex for students at the University of Wolverhampton, Victoria Hall consists of four buildings, and is a substantial architectural solution to urban housing and tight building sites in this historic English town, about 110 miles northwest of London. The tallest building of the group is of particular note because, at 25 stories, it now holds the record for overall height and number of stories in a building constructed principally off-site. The ground floor is site-built, but the other 24 stories are assembled from 383 individual modules built several hundred miles away across land and sea in Cork, Ireland.
Challenged with the multiple pressures of speed, quality, and scale, the project team investigated alternative methods of project delivery. Vision Modular Structures, a division of The Fleming Group, entered the picture. The Fleming Group is a general contractor, Vision is their modular building division. Fleming/Vision, which has completed several other modular projects in their native Ireland, was contracted to build both the modules and the site-built components. Fleming also provided general construction management.
Considering that the demands of this project in general were substantial and that this project is the first time many on the project team had worked with modular methods, it is interesting to know that when asked if they would do it again, the common response is “absolutely.”
“In spite of this being a new method for most team members, the project went smoothly, quickly, stayed on budget, maintained our quality objectives and architectural integrity, and will actually be done ahead of our originally aggressive schedule, ” says Jenny Hayes, RIBA, O’Connell East’s project architect on Victoria Hall.
It is hard to argue with that.
For the full article, click here.
© Miletus Group, Inc. 2011