AIA SD – Modular Roundtable Jan 28, 2014
Open discussion January 28, 2014.
This will be an open discussion session covering all things prefab. All AIA members are welcome to join the conversation.
Brown Bag Roundtable: Modular Architecture
Tuesday, January 28, 2014, 12-1:30 pm
AIA SanDiego Chapter Office
233 A Street, Suite 200
San Diego, CA 92101
http://www.aiasandiego.org
Modern Desert Prefab
Guest Speaker: Richard Orne, Architect
AIA San Diego Modular Architecture
Brown Bag Meeting Nov 26, 2013
With a dramatic 10 acre sweeping Borrego Springs desert site, a creative approach and a kit of prefab parts, Richard Orne, Architect designed and built his own modern desert home. An example of the best of Borrego Modern design, the house uses cutting edge systems-based construction technology to build a house that is in tune with its context.
AIA members are welcome to come hear about this impressive implementation of offsite construction from the architect/client’s perspective.
Richard Orne, Architect will share his thoughts and experiences on building with a set of systems based building tools to achieve a custom work of Architecture.
AIA members are welcome to join the meeting. Lunch will be provided by the AIA.
Brown Bag Roundtable: Modular Architecture
Tuesday, November 26, 2013 — 12:00 – 1:30PM
AIA San Diego Chapter Office
233 A Street, Suite 200
San Diego, CA 92101
http://www.aiasandiego.org
Modular and Prefab Library Working Group
AIA San Diego Modular Architecture
Brown Bag Meeting Sept 24, 2013
This will be a working group session to build shared knowledge base resources regarding architecture and prefabrication. Bring information about your favorite books, magazine articles, blog posts and other references to share on the AIA’s KnowledgeNet Modular and Prefabricated Architecture Group website (http://network.aia.org).
We will upload what we can and prepare a bibliography for the rest.
Brown Bag Roundtable: Modular Architecture
Tuesday, Sept 24, 2013 — 12:00 – 1:30PM
AIA San Diego Chapter Office
233 A Street, Suite 200
San Diego, CA 92101
http://www.aiasandiego.org
High Rise Prefab: Current Trends
Presentation and Discussion
AIA San Diego Modular Architecture Group
Brown Bag Meeting May 28, 2013
The next meeting of the AIA SD Modular BBRT will focus on current trends in prefabricated modular high rise architecture. In recent years we have seen 18, 24 and now 32 story buildings being manufactured as modules offsite. James Guthrie, AIA will give a short presentation on recent tall factory-built buildings from the UK and US. After the presentation, the meeting will be open for discussion on related issues. From structural techniques to general aesthetics, AIA members are welcome to come see examples and share their thoughts.
Brown Bag Roundtable: Modular Architecture
Tuesday, May 28, 2013 — 12:00 – 1:30PM
AIA San Diego Chapter Office
233 A Street, Suite 200
San Diego, CA 92101
http://www.aiasandiego.org
PreFab: Lessons from a Local University
AIA San Diego Modular Architecture Group
Brown Bag Meeting March 26, 2013
When a San Diego medical group wanted to expand their radiation oncology center, they sought speed and quality. To meet these goals they choose prefabrication.
AIA members are welcome to come hear about this impressive implementation of offsite construction from the client’s perspective.
Mike Engel, AIA will share his experience on this project. Mike is currently the Healthcare Studio Director at avrpstudios in San Diego. Formerly, he was the project architect for the local medical group during the design and construction of this prefab project.
AIA members are welcome to join the meeting.
Brown Bag Roundtable: Modular Architecture
Tuesday, March 26, 2013 — 12:00 – 1:30PM
AIA San Diego Chapter Office
233 A Street, Suite 200, San Diego, CA 92101
http://www.aiasandiego.org
Special PreFab Guest and Training at AIA SD Modular Architecture Brown Bag July 24-25
Special Guest: Researcher, Educator and Author Ryan Smith
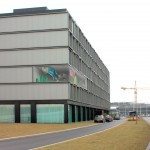
Modular Hotel Netherlands
(c) James B. Guthrie, AIA
Ryan Smith, author of PreFab Architecture (Wiley 2010) and Professor of Architecture at U of Utah, will be attending the July meeting of AIA SD’s Brown Bag Round Table discussion of modular and prefabricated architecture. This meeting will be a casual and open discussion format. Come and share your questions and experiences on the current and future state of prefabrication in architecture. Topics to include the prefabrication process in design and building, lean construction, green building, integrated technologies, global developments and more. For more information: http://www.aiasandiego.org
You are also invited to attend Prof. Smith’s more formal Offsite Design Workshop on Wednesday July 25 at the AGC training facilities in San Diego. This is a half-day morning seminar that will provide more detailed information on prefabrication in architecture and building. AIA members can earn 5 continuing education LUs. For more information: http://www.prefabeducation.com/Prefab_Education/San_Diego.html
All AIA members and allied building professionals are welcome to join these meetings.
Brown Bag Roundtable: Modular Architecture
Tuesday, Tuesday July 24, 2012 — 12:00 – 1:30PM
AIA SD Offices, 233 A Street, Suite 200, San Diego, CA
Offsite Design Workshop (5 AIA LU’s)
Wednesday July 25, 2012 — 8:00 – 12:00PM
AGC Training Facility, 6212 Ferris Square, San Diego, CA
Zero Net Energy Classroom at Modular Architecture Group
Zero Net Energy Classroom at Modular Architecture Brown Bag Group meeting Jan 31, 2012 in San Diego
The discussion will include American Modular Systems’ CHPS verified and award winning zero net energy Gen7 modular classroom.
January’s guest will be Jim Wallace of AMS. AMS is a California manufacturer of commercial, institutional, and modular buildings.
All AIA members are welcome to join the meeting.
Brown Bag Roundtable: Modular Architecture
Tuesday, January 31, 2012 — 12:00 – 1:30PM
AIA San Diego Chapter Office
© Miletus Group, Inc. 2012
Modular Architecture Group
AIA Meeting Dec 6, 2011 in San Diego
Q: What do the Marmol-Radziner Desert House, the Sunset Breeze House, the WIRED Livinghome and High Tech High all have in common?
A: They are all modular and they were all engineered by the modular experts RS Tavares Associates!
Come hear Ralph Tavares, PE share his insights into these and other special modular buildings at the next Brown Bag Roundtable on Modular Architecture.
All AIA members welcome. For more information, link here.
Brown Bag Roundtable: Modular Architecture
December 6, 2011
12-130pm
San Diego AIA
If you are unable to attend this meeting, consider joining the The Modular and Prefabricated Architecture Group on the AIAKnowledgeNet.
© Miletus Group, Inc. 2011
McGraw Hill: Prefabrication and Modularization
McGraw Hill Construction’s recent publication of “Prefabrication and Modularization: Increasing Productivity in the Construction Industry” provides a deep look into current thinking and trends surrounding off-site construction in the US. Overall, the report is very good and worth taking the time to read and ponder the implications of its contents.
While it is a bit disappointing that McGraw Hill did not tackle the important but less tangible aspects of architecture and design, the contents do provide the reader with a broad understanding of the benefits of this method of construction. Architects who read it won’t walk away with an immediate or complete tool set for how to design buildings for off-site construction, but, and this is also important, they will have a few more heavy duty tools for talking to their clients about it as an option for their upcoming architectural projects. According to the report, the number one reason that off-site is not used on more building projects is because “the architect did not design it into the project.”
Why should architects care? The report does a very good job of answering this question. According to McGraw Hill’s research, prefabrication and modularization offers the building process many improvements in a number of key fronts. These include:
- Improved Project Schedules
- Reduced Cost and Budgets
- Site Safety
- Green Building and Waste Reduction
The report goes into great detail about its findings in these areas. If you want some tools to learn about and be able to talk to the issues of increasing construction productivity, we invite you to read the report for yourself.
– – –
The Modular Building Institute Educational Foundation is offering a limited number of full color printed editions this report in exchange for a $100 or more tax-deductible donation to the Foundation. You can contact us through the comment area if you would like to make a donation and receive a copy/copies of the report.
© Miletus Group, Inc. 2011
McGraw Hill: Increasing Productivity in the Construction Industry
McGraw Hill Construction recently published a document called: “Prefabrication and Modularization: Increasing Productivity in the Construction Industry.”* This is the latest in their Smart Market Reports, a series they publish on construction industry trends.
A lot of research went into the report and it contains many interesting sub-topics. However, it only takes a quick look at the cover to find the first item of note. The report’s sub-title is: “Increasing Productivity in the Construction Industry.”
Most people who work in the construction industry are keenly aware that traditional site-built methods of construction have a bad reputation when it comes to efficiency. Likewise, most building owners and developers are keenly aware that those efficiencies hit the pocket book hard as they manifest themselves as poor quality work, change orders and completion delays. That McGraw Hill chose to include off-site construction in the general discussion of how we build all buildings is a huge step in the right direction of understanding that there is a better option in the way we create and assemble buildings.
This is a significant notion. Most non-industry discussions about prefabrication tend to see it as an anomaly, a mere curiosity for small scale players. They relinquish ‘prefab’ to the sidelines of the greater discussion of how we build all buildings, big and small. Those of us who currently practice in the off-site industry understand how efficient this method of construction really is and generally have a large vision of how important a role it can play in curing the productivity woes found with on-site construction. That McGraw Hill decided to take this on with an in depth analysis is in itself worthy of mention.
* While primarily researched and published by McGraw Hill, this Smart Market report included a number of partners. One partner was the Modular Building Institute Educational Foundation, of which James B. Guthrie, AIA, President of Miletus Group, is the Chair.
– – –
The Modular Building Institute Educational Foundation is offering a limited number of full color printed editions this report in exchange for a $100 or more tax-deductible donation to the Foundation. You can contact us through the comment area if you would like to make a donation and receive a copy/copies of the report.
© Miletus Group, Inc. 2011
Modular Architecture Brown-Bag Roundtable
AIA Meeting August 2, 2011 in San Diego
Find out more about the latest methods in modern, modular construction. It’s not just theory; it’s winning prestigious design awards for architects interested in sustainable building, cost efficiency and quality control.
Come to the next meeting of the Modular Architecture Brown Bag group to hear Eric Naslund, FAIA of Studio E Architects discuss his project: High Tech High. Eric will be sharing his experiences using modular construction in his COTE award-winning design.
Modular Brown-Bag Roundtable
August 2, 2011
12:00 pm – 1:30 pm
AIA San Diego
233 A Street, #200
San Diego, CA 92101
Phone: (619) 232-0109
Email: info@aiasandiego.org
Increasing interest and the recent growth in the US and abroad of new construction substantial modular buildings, and the industries surrounding it, signifies a significant change on the architectural landscape. At the National AIA level, on the new AIAKnowledgeNet, The Modular and Prefabricated Architecture Group has been established to provide a central location where architects and allied professionals can share, learn and promote state-of-the-art offsite construction to new architectural levels.
AIA San Diego invites you to join your peers who share your interest in this topic at a local Brown-Bag Roundtable. No RSVP is necessary. This is a free, member-only, bring-your-own-brown-bag event. Food vendors are available in the building for those wishing to purchase their lunch.
High Tech High
Jim Brady Architectural Photography
High Tech High Modules
© Miletus Group, Inc. 2011
Miletus Group Returns to its Roots! Opens Chicago Architectural Office
Miletus Group has officially announced the opening of its new office in Chicago, IL at 2823 N. Milwaukee Avenue, Suite E, (312) 265-6447. The new Chicago metropolitan location will house architectural services, building on the continued success of the Miletus Group management, design, and production operations in its Rochester, IN headquarters.
“The new design office gives us a great new platform to reach out to the entire Chicago metropolitan market,” says James B. Guthrie, AIA, president of Miletus Group, adding, “We have exciting plans for innovative, large-scale modular solutions involving hotel, apartment, and healthcare facility projects,” he further explains. “Chicago is a natural market for substantial building in these sectors, making it a perfect fit for our future growth strategy. In addition, Chicago is my hometown, so I very much look forward to working there with our staff of talented architects.”
Chicago was selected as a key growth market, according to Guthrie, because of its proximity to the company’s production facility in Indiana, and because it provides a large market area with a history of progressive thinking in terms of architecture and building. Guthrie points out that early in the twentieth century, Chicago-founded Sears, Roebuck and Co. sold over 70,000 precut and prepackaged homes through their mail order Modern Homes program, which allowed customers to choose a house to suit their individual tastes and budgets. At approximately the same time, he goes on to explain, Frank Lloyd Wright introduced his textile block Usonian home concept to demonstrate that exceptional quality and design, using prefabricated components, can be made available to the masses.
“Conceptually, we stand on the shoulders of such Chicago icons as Sears and Frank Lloyd Wright, who paved the way for modular architecture,” Guthrie states. “Today, we are seeing a resurgence in modular architecture,” he continues. “The interest is driven in small part by economics, but more so by a desire for greener construction practices, creative design, and the caliber of high quality production that Miletus Group consistently delivers and will now extend into the Chicago market.”
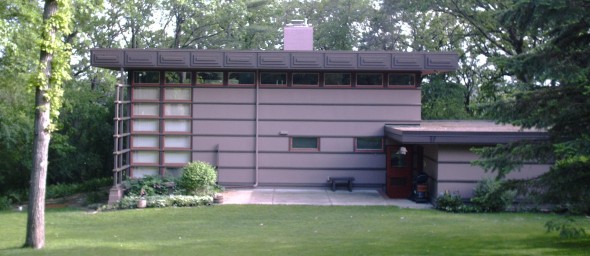
Frank Lloyd Wright McBean House in Rochester, Minnesota. This Usonian house is an example of the second type (Prefab #2) of the Marshall Erdman Prefab Houses.
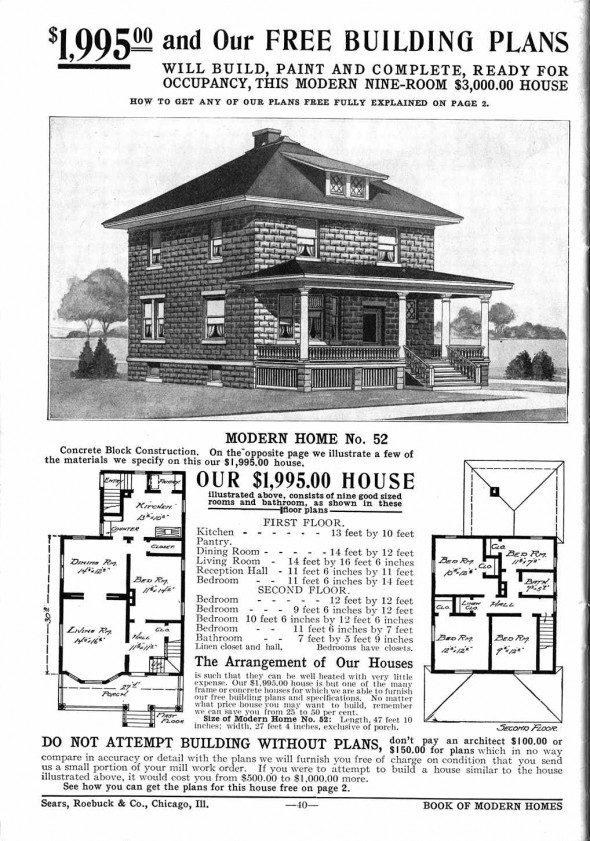
Sears Homes 1908 – 1914, Chicago, IL From the Sears Archives Model No. 52
Miletus Group’s Shotgun Project featured in Residential Architect Magazine
Miletus Group’s innovative Hurricane Katrina housing solution, named The Shotgun Project, was featured in the May/June issue of Residential Architect. According to Residential Architect, “Hurricane Katrina and the ensuing flooding left New Orleans with a significant housing crisis that has not yet been resolved. Rochester, Ind.–based design/build firm Miletus Group, which specializes in prefab and modular systems, has developed a prototype that may help.”
“These ingenious modular structures are substantial homes,” Miletus president James B. Guthrie, AIA notes, “fully compliant with current building codes and FEMA standards, offering a sustainable, permanent solution to the current and near-term housing needs of New Orleans.”
Click on the image below to read the entire article online.
Miletus NEWS: The Green Fleet marks industry’s first eco-friendly mobile field office fleet
Miletus Group, Inc. has joined forces with Jobsite Leasing Company to make mobile and modular offices eco-friendly. The Green Fleet™ marks a first in the industry, which has lagged behind conventional commercial building in terms of sustainable building practices. Mobile field offices, long a staple of the construction industry and present on virtually every construction site of medium and large construction projects around the world, are easily ignored as a ‘real’ building type.
When energy costs associated with the use and operation of Jobsite’s fleet of mobile and modular field offices started generating customer comment Jobsite decided to examine the possibilities of developing a green mobile building with the modular design experts at Miletus Group.
Miletus Group accepted the challenge. Miletus Group president and project spokesperson James B. Guthrie, AIA points out, “Our team spent a great deal of time analyzing the best sustainability practices in the building industry and then found ways to apply them to the mobile and modular office building sector.” Little will appear changed to office occupants in terms of the general layout, construction, and convenience of the high performance units, according to Guthrie. However, he states noticeable differences will appear in the form of substantially lower utility bills and significantly higher levels of comfort during hot summer and frigid winter months.
When asked why an architectural firm would be interested in a mobile office, Guthrie said: “If we were talking about one field office, one does have to wonder if the effort is worth creating 700 square feet of high performance building. However, our client is a fleet operator. They asked us to examine creating an entire fleet of these buildings. One’s perspective changes significantly when you add them all up.” According to the Modular Building Institute, there are approximately 300,000 fleet field offices in North America alone. That number represents over 200,000,000 square feet of green building potential. Guthrie added, “Doing this project felt a lot like planting the first tree in the creation of a forest. I might not get to sit in all that shade, but future generations sure will.”
Because this industry is highly cost driven, Jobsite first commissioned Miletus Group to perform a cost analysis to determine the feasibility of building high performance mobile and modular offices. Guthrie and his team began by doing alternative preliminary designs and then running a series of Department of Energy and USGCB LEED approved building performance computer models. The models provided a baseline analysis of the existing fleet against alternative design approaches. The results quickly proved that energy savings would offset initial green building costs. “The computer models were invaluable in assessing different approaches and creating a strategy for building procedures,” says Guthrie. With the help of the computer models, the manufacturer incorporated refinements in materials and production, which led to new efficient and cost-effective sustainable practices in the building of the High Performance Mobile Offices™, and a greater than 50 percent reduction in energy use. With the help of the Miletus design team, Jobsite was also able to dramatically reduce construction material waste, 95 percent of which is now recyclable. Additionally, the materials selection process was overhauled to include purchasing only from vendors that offer the largest inventory and highest degree of recyclable products on the market. The green building measures assured that the High Performance Mobile Offices would be 100 percent recyclable at the end of its life cycle. Moreover, Guthrie, who counts among his green building credentials, certified Green Advantage practitioner for commercial and residential construction, U.S. Green Building Council member, and member of the Modular Building Institute’s International Green Code review committee, expects ongoing field-monitoring reports will show building energy usage of sustainable-built High Performance Mobile Offices to be as little as one-third that of conventionally built, standard industry mobile offices.
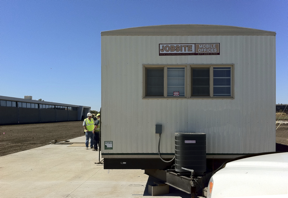
On site at the USGBC LEED Platinum Transpo Center in South Bend, IN

HPMO, like a tree to a forest
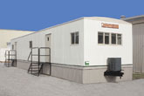
HPMO with recommended insulated skirting
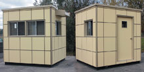
Full scale field office prototypes
© Miletus Group, Inc. 2011