Prefab: Global Affordable Housing Solutions
Speaker:
James B. Guthrie, AIA
Miletus Group, Inc.
The global need for affordable housing is massive and growing rapidly. India alone estimates that they currently have a housing shortage of over 18 million dwelling units, and that number continues to grow. China and many African nations are in a similar condition with population growth fast out pacing housing production. Skilled construction labor is in short supply.
Working with an international consortium, James B. Guthrie, AIA, president of Miletus Group, Inc., has developed designs and a design-build strategy to bring the benefits of prefabrication and modern methods of construction to worldwide areas of need.
James will share the story of the design, its design-build process, and how this international team came together to offer a new scheme for building worldwide affordable housing.
Brown Bag Roundtable: Modular Architecture
Tuesday, March 25, 2014 — 12:00 – 1:30PM
AIA San Diego Chapter Office
233 A Street, Suite 200
San Diego, CA 92101
http://www.aiasandiego.org
ACSA Offsite Conference in Philadelphia
Offsite Conference was Historic
The Association of Collegiate Schools of Architecture (ACSA) recently (September 27-29, 2012) concluded their fall conference Offsite: Theory and Practice of Architectural Production in Philadelphia. Miletus Group was proud to sponsor the keynote address: Offsite in the UK. It was given by Jaimie Johnston, Director at Bryden-Wood, London. Miletus President James B. Guthrie, AIA also moderated a couple of panels and attended a number of the papers given. Schools from all over the US and several other countries were represented as both presenters and attendees.
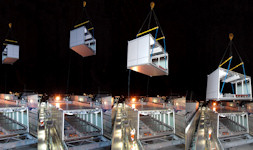
Bryden-Wood
BAA Airport Corridor Product
The depth of the research and conversation was impressive. This may be the first time so much brain power has been singularly focused on the discussion of the past, present and future of offsite and prefabricated construction methods in architecture. It gives one hope that the architectural community is embracing this method of construction with a greater depth of interest and knowledge than it ever has before. In the past we have seen some dabbling by some famous and not so famous architects, but at the ACSA conference there was a very real depth and breadth to the conversation of offsite as an architectural solution. It remains to be seen if this event will be The inflection point of offsite moving from an architectural novelty to an integrated part of the building of architecture, but it may very well be.
As Guthrie pointed out in his keynote introduction: “If we look at the long history of iron and steel in architecture, we see its roots as a non-architectural structural building material at the beginning of the 19th Century. At that time it was embraced by structural and cost engineers. 80 years later, a French bridge engineer caught the world’s imagination by building the functionless yet dramatic Eiffel Tower. About that same time Jennings and Sullivan were in Chicago developing the first architectural expressions based on iron. It took another 40 years until Mies turned it into poetry. In the historic arc of offsite construction, we are at the time of Sullivan. The coming years should prove very exciting as architects learn to use and exploit offsite.”
The papers from the ACSA fall conference on Offsite will be published soon.
For more on ACSA: http://www.acsa-arch.org
Modular Architecture Q&A: New Materials or Technologies
Below is the next post, number 5, in the continuing series of prefab/modular Q&A asked by Norman Gray, a graduate student at the New School of Architecture and Design in San Diego, CA and answered by James B. Guthrie, AIA, President of Miletus Group, Inc.
Question:
Are there any new materials or technologies which are making prefab construction more cost effective?
Answer:
As far as I am aware, no none that directly pertain to offsite construction.
There are some new building materials on the horizon that show promise, but as of yet they have not made it into prefab production. At this time, the cost benefit of prefab is in the process, not the materials. This could easily change in the near future as the supply chain becomes more robust, but for now the focus has been on tweaking standard methods to make building more cost effective.
Manufacturing processes that allow repetitive work to be done quickly is the chief driver of prefab right now. Quick assembly once on the site is another. Use of sustainable building practices is yet another. Perhaps one aspect of using manufactured processes that is a new benefit to the building world is the idea of greater precision in building. Products produced in a factory setting are inherently built more accurately than on site work. This can translate into stronger and more efficient buildings. The application of the methodology to architecture is somewhat new. The building materials and technologies, however, still tend to parallel standard construction.
Related link: http://www.newschoolarch.edu
© Miletus Group, Inc. 2012
Modular Architecture Q&A: Time and Money
James B. Guthrie, AIA, the President of Miletus Group, Inc, was recently approached by Norman Gray, a graduate student at the New School of Architecture and Design in San Diego, CA regarding an architectural project he was working on. As a part of his research, Mr. Gray sought our expertise in answering several questions regarding prefab and modular construction. We thought the questions were very good ones and worth sharing with a wider audience. We will post each question and answer as a separate blog post. Readers who have their own questions about modular architecture are encouraged to ask us as well.
Question:
What percentage of time and money do you think prefab can save a project?
Answer:
When it comes to prefab, generalized questions can be difficult to answer. In general, on a direct apples-to-apples comparison, I would say that you could expect that a prefab project can be 0-15% less per square foot than a traditionally built project of the same design and specifications. There are too many variables, though, to allow a hard and fast rule as to discounts.
It is also important to keep in mind that when we are talking about prefab, we can be talking about prefab architecture or prefab building. When I talk about prefab architecture, I am using the idea that architecture is a high quality building designed by a professional and it is always site specific. This means that each prefab architecture project will be unique to the site it is being placed on. The quality of the end result will be high quality, and the owner will be a ‘client’ of a professional architect. Prefab building, in contrast, is a generic ‘product’ that can be non-site specific. The quality can vary dramatically from project to project and the owner of this product is a customer of a building company.
The other important thing to consider is the definition of “project”. Architects tend to think of a project as the specific building they are working on. Building owners, however, think of a “project” as the entire business model related to that building. This includes the architecture plus: land acquisition and development, operations and maintenance, financing, cash flow and other business considerations. To answer the question about prefab architecture from the architect’s side, at this time a prefab architecture project has no inherent time or money advantages to the architect except as it may add value for their clients. To answer the question from the owner’s perspective regarding prefab architecture, it can have significant time savings, which to the owner can translate into a huge financial savings to the non-architectural aspects of the project. The amount of savings is, of course, dependent on the project.
Typical Modular Home, USA
2 Offsite Stories, 1 Single Family House, 4 Modules
On the small scale, in the US right now it is very easy for a homebuyer to buy a house much like they buy a car. The homebuyer can go to a sales lot of a manufactured home builder, tour model homes, pick out their model, pick out colors and finishes, and have their new home delivered in a very short amount of time. These homebuyers are buying a prefab building, not prefab architecture. The opportunity for this kind of building to become architecture is very limited. Because prefabrication is a method of construction that takes advantage of manufacturing processes, the economic side of prefab is most successful when there is volume on the production side. One single family home does not afford current manufacturing processes the kind of efficiencies needed to be cost effective. In the case of a home or small commercial building, volume is achieved when many of the same design are produced. In this situation, the efficiency is dispersed among many buyers. This means, naturally, that each individual buyer looses the opportunity to influence the design and quality of their purchase.
Modular Housing, England
10 Offsite Stories, 162 Apartments, 630 Modules
On the large scale, the prefab building buyer is also buying the convenience of speed to occupancy, but the larger scale can allow the project to be more architectural. Fundamentally the building process is relatively the same between prefab and onsite construction, except that the offsite components can be built simultaneously with much of the onsite work. The onsite assembly of the offsite components can then occur very rapidly. On a large project this can save a lot of time, and thus a lot of money to the owner. This is important, as even if the square footage costs of onsite and offsite construction are nearly identical, the cost savings to the owner can be very significant and far exceed the 0-15% savings in square footage costs. Unlike a single family home, the size of a large project can allow the design to take on far more significant role than is possible in small projects. It is the large projects that create the greatest opportunity for all the benefits of prefabrication and the application of real architecture to meld. This is the future of prefabrication in architecture.
Related link: http://www.newschoolarch.edu
© Miletus Group, Inc. 2011
Jobsite Mobile Office’s® Green Fleet® will be a featured attraction at the BCA Construction and Design Expo – Indiana’s largest construction trade show
The Green Fleet represents the world’s first eco-friendly HPMO (High Performance Mobile Office®) developed by the Miletus Group for Jobsite Mobile Offices. Jobsite Mobile Offices will feature the new Green Fleet HPMO at the BCA Construction and Design Expo – September 28-29, 2011 – Memorial Coliseum Exposition Center – Fort Wayne, Indiana. The 1260 HPMO will be located at the show entrance and will be fully furnished, manned, and powered.
Designed by the modular architecture specialists at Miletus Group, Inc., the HPMO installation is a pinnacle part of Jobsite Mobile Office’s 40th anniversary celebration taking place at the show.
About the Green Fleet HPMO Design
“We are proud of the work we did in partnership with Jobsite,” states James B. Guthrie, AIA, Miletus Group president. “The revolutionary HPMO uses at least one third less energy than conventional mobile offices. Some customers are reporting energy savings of well over 50%. This new thinking in mobile office design also includes a high level of recycled materials and is 100% recyclable at the end of its long life cycle. Our team spent a great deal of time analyzing the best sustainability practices in the building industry and then found ways to apply them to the mobile and modular office-building sector. Little will appear changed to office occupants in terms of the general layout, construction, and convenience of the high performance units. However, noticeable differences will appear in the form of substantially lower utility bills and significantly higher levels of comfort during hot summer and frigid winter months,” says Guthrie.
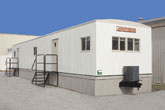
The Jobsite Green Team celebrates their 40th Anniversary at the BCA Construction and Design Expo. The Miletus Group designed the innovative HPMO to be featured at the Expo.
Miletus Group’s new Chicago office featured on Inside Indiana
Inside Indiana featured Miletus Group’s expansion to the Chicago area and quoted president James Guthrie stating, “The move is a good fit because of its proximity to the company’s headquarters and history of architectural innovation.” For more on the move, please link to the article here to read on.
Modular Architecture Brown-Bag Roundtable
AIA Meeting August 2, 2011 in San Diego
Find out more about the latest methods in modern, modular construction. It’s not just theory; it’s winning prestigious design awards for architects interested in sustainable building, cost efficiency and quality control.
Come to the next meeting of the Modular Architecture Brown Bag group to hear Eric Naslund, FAIA of Studio E Architects discuss his project: High Tech High. Eric will be sharing his experiences using modular construction in his COTE award-winning design.
Modular Brown-Bag Roundtable
August 2, 2011
12:00 pm – 1:30 pm
AIA San Diego
233 A Street, #200
San Diego, CA 92101
Phone: (619) 232-0109
Email: info@aiasandiego.org
Increasing interest and the recent growth in the US and abroad of new construction substantial modular buildings, and the industries surrounding it, signifies a significant change on the architectural landscape. At the National AIA level, on the new AIAKnowledgeNet, The Modular and Prefabricated Architecture Group has been established to provide a central location where architects and allied professionals can share, learn and promote state-of-the-art offsite construction to new architectural levels.
AIA San Diego invites you to join your peers who share your interest in this topic at a local Brown-Bag Roundtable. No RSVP is necessary. This is a free, member-only, bring-your-own-brown-bag event. Food vendors are available in the building for those wishing to purchase their lunch.
High Tech High
Jim Brady Architectural Photography
High Tech High Modules
© Miletus Group, Inc. 2011
Miletus Group Returns to its Roots! Opens Chicago Architectural Office
Miletus Group has officially announced the opening of its new office in Chicago, IL at 2823 N. Milwaukee Avenue, Suite E, (312) 265-6447. The new Chicago metropolitan location will house architectural services, building on the continued success of the Miletus Group management, design, and production operations in its Rochester, IN headquarters.
“The new design office gives us a great new platform to reach out to the entire Chicago metropolitan market,” says James B. Guthrie, AIA, president of Miletus Group, adding, “We have exciting plans for innovative, large-scale modular solutions involving hotel, apartment, and healthcare facility projects,” he further explains. “Chicago is a natural market for substantial building in these sectors, making it a perfect fit for our future growth strategy. In addition, Chicago is my hometown, so I very much look forward to working there with our staff of talented architects.”
Chicago was selected as a key growth market, according to Guthrie, because of its proximity to the company’s production facility in Indiana, and because it provides a large market area with a history of progressive thinking in terms of architecture and building. Guthrie points out that early in the twentieth century, Chicago-founded Sears, Roebuck and Co. sold over 70,000 precut and prepackaged homes through their mail order Modern Homes program, which allowed customers to choose a house to suit their individual tastes and budgets. At approximately the same time, he goes on to explain, Frank Lloyd Wright introduced his textile block Usonian home concept to demonstrate that exceptional quality and design, using prefabricated components, can be made available to the masses.
“Conceptually, we stand on the shoulders of such Chicago icons as Sears and Frank Lloyd Wright, who paved the way for modular architecture,” Guthrie states. “Today, we are seeing a resurgence in modular architecture,” he continues. “The interest is driven in small part by economics, but more so by a desire for greener construction practices, creative design, and the caliber of high quality production that Miletus Group consistently delivers and will now extend into the Chicago market.”
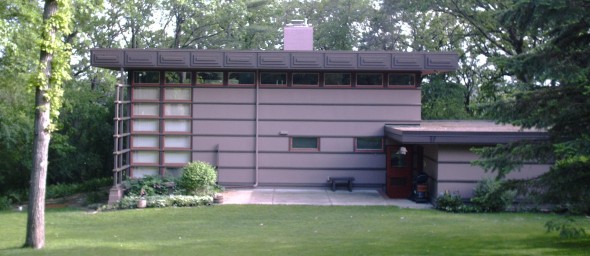
Frank Lloyd Wright McBean House in Rochester, Minnesota. This Usonian house is an example of the second type (Prefab #2) of the Marshall Erdman Prefab Houses.
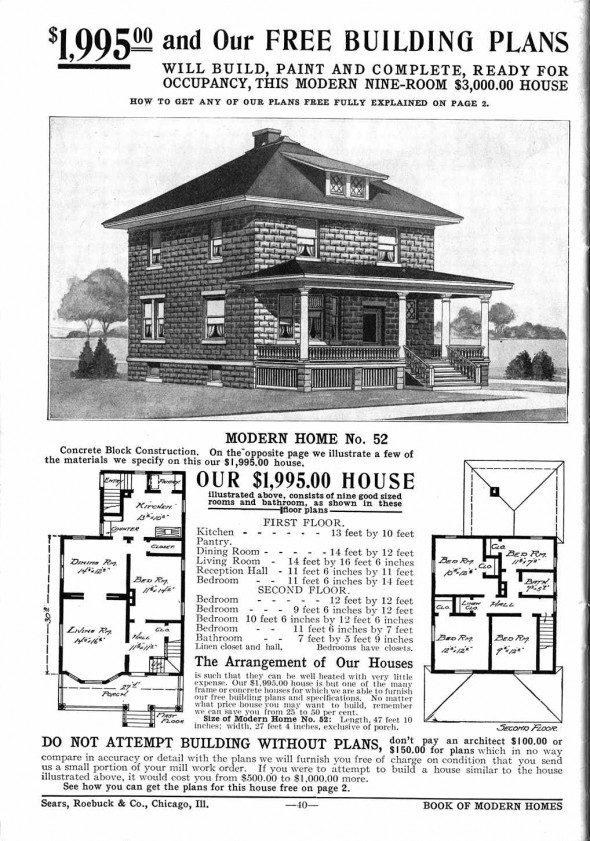
Sears Homes 1908 – 1914, Chicago, IL From the Sears Archives Model No. 52
Miletus Group’s Shotgun Project featured in Residential Architect Magazine
Miletus Group’s innovative Hurricane Katrina housing solution, named The Shotgun Project, was featured in the May/June issue of Residential Architect. According to Residential Architect, “Hurricane Katrina and the ensuing flooding left New Orleans with a significant housing crisis that has not yet been resolved. Rochester, Ind.–based design/build firm Miletus Group, which specializes in prefab and modular systems, has developed a prototype that may help.”
“These ingenious modular structures are substantial homes,” Miletus president James B. Guthrie, AIA notes, “fully compliant with current building codes and FEMA standards, offering a sustainable, permanent solution to the current and near-term housing needs of New Orleans.”
Click on the image below to read the entire article online.
Miletus Group’s green modular solutions featured in Building Indiana News
Miletus Group’s HPMO and Jobsite Leasing’s Green Fleet was featured in Building Indiana News in an article about new mobile and modular solutions. Click on the image below to read the article online – page 58. According to Building Indiana, “Miletus Group and Jobsite Leasing Company have created the mobile office industry’s first green options.” For more on the project, link to our previous blog story here.
Miletus Group Develops an Architecturally Appealing Rescue Strategy for New Orleans’ Post-Katrina Housing Crisis
The modular design experts at architecture firm Miletus Group, Inc. have been selected by a prominent housing developer and landowner to develop their Shotgun House Project™—a historically and architecturally sensitive approach to quickly address New Orleans’ post-Katrina housing crisis. After extensive project prototype work, the first Shotgun House model has been designed for an Uptown lot and is slated for completion this year.
Miletus Group’s Shotgun Homes are architectural-quality, permanent modular buildings designed to fit into New Orleans’ neighborhoods as if they had been there for a century or more. These ingenious modular structures are substantial homes, fully compliant with current building codes and FEMA standards, offering a sustainable, permanent solution to the current and near-term housing needs of New Orleans.
“Hurricane Katrina’s lasting effects have created a massive housing deficit in New Orleans,” states Miletus Group president James B. Guthrie, AIA. “This housing dilemma is exacerbated by labor shortages and the high price of available building materials. Our premise was to build high quality, and architecturally sensitive homes off site, away from the stresses of New Orleans’ building environment. These modular buildings could then be put in place quickly, reducing time to occupancy, and alleviating much of the inconvenience and noise pollution in the neighborhoods where they are being constructed.” Miletus is renowned for their sustainable building expertise, particularly in modular structures.
The Shotgun Project offers a variety of home options, from fully completed and ready-for-occupancy, to fully customizable homes that are left partially unfinished as a more affordable choice for more handy do-it-yourselfers in need of immediate shelter. “The innovative Shotgun House design recalls the past, while providing comfortable, modern housing for its occupants,” states Guthrie. “It is a durable and permanent solution for a desirable housing type that is based on generations of New Orleans history and precedent.”
For more information, contact Miletus Group, Inc.
© Miletus Group, Inc. 2011
Miletus Group Takes First Place Honors at MBI 2011 Awards of Distinction.
Miletus Group took home first place honors in the Modular Building Institute (MBI) Awards of Distinction.
The Awards of Distinction is the largest international contest of mobile and modular buildings. The program seeks the best of the best in commercial modular building entries submitted by MBI member companies. A notable panel of judges from the architectural and building community reviews them. Judges look for exceptional projects in the areas of architectural excellence, technical innovation, efficiency, and length of project delivery.
Miletus Group’s Jobsite project won in the Temporary structure category with a highly sustainable mobile field office and used at the nation’s first LEED™ Platinum transit facility. This singlewide mobile field office, built on a standard 1260 frame, provides the same functional and mobility advantages as a traditional mobile field office – but with clever design and technical innovations that add up to a huge reduction in the client’s fleet’s overall carbon footprint.
This unit represents the culmination of two years of research and development into how to apply the most advanced green building measures into a production line and a fleet of lease fleet units. While the unit does include the latest in low energy lighting, HVAC equipment and related technologies, the real performance enhancements come from its sophisticated thermal skin.
The cost effectiveness and energy efficiency of this unit comes in several levels:
- First, the unit has been designed for ultimate production ease and efficiency to manufacture.
- Second, the material choices were selected for their durability, providing a long-term life and a higher than standard ROI.
- Third, virtually all of the materials used in the unit are recyclable. This makes decommissioning more cost effective, requires no land fill space, and lowers the end of life energy use and thus its overall carbon footprint.
- Fourth, the day-to-day performance of the unit, due to its efficient systems and enhanced skin, greatly reduce the operational energy use by up to 70% of a standard unit when all end-user options are incorporated.
© Miletus Group, Inc. 2011
Miletus NEWS: The Green Fleet marks industry’s first eco-friendly mobile field office fleet
Miletus Group, Inc. has joined forces with Jobsite Leasing Company to make mobile and modular offices eco-friendly. The Green Fleet™ marks a first in the industry, which has lagged behind conventional commercial building in terms of sustainable building practices. Mobile field offices, long a staple of the construction industry and present on virtually every construction site of medium and large construction projects around the world, are easily ignored as a ‘real’ building type.
When energy costs associated with the use and operation of Jobsite’s fleet of mobile and modular field offices started generating customer comment Jobsite decided to examine the possibilities of developing a green mobile building with the modular design experts at Miletus Group.
Miletus Group accepted the challenge. Miletus Group president and project spokesperson James B. Guthrie, AIA points out, “Our team spent a great deal of time analyzing the best sustainability practices in the building industry and then found ways to apply them to the mobile and modular office building sector.” Little will appear changed to office occupants in terms of the general layout, construction, and convenience of the high performance units, according to Guthrie. However, he states noticeable differences will appear in the form of substantially lower utility bills and significantly higher levels of comfort during hot summer and frigid winter months.
When asked why an architectural firm would be interested in a mobile office, Guthrie said: “If we were talking about one field office, one does have to wonder if the effort is worth creating 700 square feet of high performance building. However, our client is a fleet operator. They asked us to examine creating an entire fleet of these buildings. One’s perspective changes significantly when you add them all up.” According to the Modular Building Institute, there are approximately 300,000 fleet field offices in North America alone. That number represents over 200,000,000 square feet of green building potential. Guthrie added, “Doing this project felt a lot like planting the first tree in the creation of a forest. I might not get to sit in all that shade, but future generations sure will.”
Because this industry is highly cost driven, Jobsite first commissioned Miletus Group to perform a cost analysis to determine the feasibility of building high performance mobile and modular offices. Guthrie and his team began by doing alternative preliminary designs and then running a series of Department of Energy and USGCB LEED approved building performance computer models. The models provided a baseline analysis of the existing fleet against alternative design approaches. The results quickly proved that energy savings would offset initial green building costs. “The computer models were invaluable in assessing different approaches and creating a strategy for building procedures,” says Guthrie. With the help of the computer models, the manufacturer incorporated refinements in materials and production, which led to new efficient and cost-effective sustainable practices in the building of the High Performance Mobile Offices™, and a greater than 50 percent reduction in energy use. With the help of the Miletus design team, Jobsite was also able to dramatically reduce construction material waste, 95 percent of which is now recyclable. Additionally, the materials selection process was overhauled to include purchasing only from vendors that offer the largest inventory and highest degree of recyclable products on the market. The green building measures assured that the High Performance Mobile Offices would be 100 percent recyclable at the end of its life cycle. Moreover, Guthrie, who counts among his green building credentials, certified Green Advantage practitioner for commercial and residential construction, U.S. Green Building Council member, and member of the Modular Building Institute’s International Green Code review committee, expects ongoing field-monitoring reports will show building energy usage of sustainable-built High Performance Mobile Offices to be as little as one-third that of conventionally built, standard industry mobile offices.
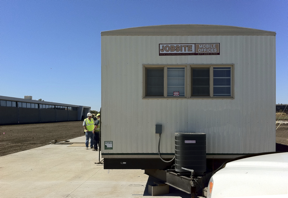
On site at the USGBC LEED Platinum Transpo Center in South Bend, IN

HPMO, like a tree to a forest
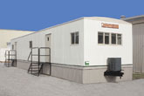
HPMO with recommended insulated skirting
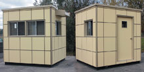
Full scale field office prototypes
© Miletus Group, Inc. 2011
Welcome
Welcome to the new Miletus: Architecture + blog.
We hope to have many interesting posts in the near future, but let’s start with a bit of wisdom that ties our name, our profession, our approach and our banner altogether in one guiding thought:
“A society grows great when old men plant trees whose shade they know they shall never sit in.”
– Ancient Greek Proverb
© Miletus Group, Inc. 2011