PreFab: Lessons from a Local University
AIA San Diego Modular Architecture Group
Brown Bag Meeting March 26, 2013
When a San Diego medical group wanted to expand their radiation oncology center, they sought speed and quality. To meet these goals they choose prefabrication.
AIA members are welcome to come hear about this impressive implementation of offsite construction from the client’s perspective.
Mike Engel, AIA will share his experience on this project. Mike is currently the Healthcare Studio Director at avrpstudios in San Diego. Formerly, he was the project architect for the local medical group during the design and construction of this prefab project.
AIA members are welcome to join the meeting.
Brown Bag Roundtable: Modular Architecture
Tuesday, March 26, 2013 — 12:00 – 1:30PM
AIA San Diego Chapter Office
233 A Street, Suite 200, San Diego, CA 92101
http://www.aiasandiego.org
Modular Architecture Q&A: Project Size vs Economics
Below is the next post, number 3, in the continuing series of prefab/modular Q&A asked by Norman Gray, a graduate student at the New School of Architecture and Design in San Diego, CA and answered by James B. Guthrie, AIA, President of Miletus Group, Inc.
Question:
Is there a minimum size for a project to make prefab economically viable?
Answer:
No. Prefab is a generic concept that has been used to make buildings as small as garden sheds (1 small module) and as large as a 24 story apartment building (500+ large modules). Viability is determined by all the factors that go into making the building, including understanding the supply chain that produces the factory made components and the efficiencies inherent in that chain.
In the case of the garden shed, the sheds are standard designs produced by the hundreds, if not thousands. In the case of the 24 story building, the resulting building is a single architectural structure. One commonality that lead to the economic success in both examples is the use of repetition where repetition made sense. In the case of the garden shed, repetition is probably obvious as each shed is a copy of a singular design. In the example of the 25 story building, the architect cleverly exploited repetition in the layout of the apartments so that very few unique modules were used yet an overall creative architectural solution was achieved.
The fundamental lesson of economic viability here is that if you want to use prefab for a small building, make many replicas of the same building. If you want to use prefab for a large building, make it from many similar components.
Related link: http://www.newschoolarch.edu
© Miletus Group, Inc. 2011
Modular Architecture Q&A: Transportation Costs
Below is the second post in the continuing series of prefab/modular Q&A asked by Norman Gray, a graduate student at the New School of Architecture and Design in San Diego, CA and answered by James B. Guthrie, AIA, President of Miletus Group, Inc.
Question:
Is transportation of prefab/modular units a significant cost factor?
Answer:
The general answer would be ‘yes’, but how significant is dependent on the details of the project. These details include: the distance and travel conditions between the project and the factory, the size and weight of the prefab components, and the cost of labor at the two locations. To illustrate the extremes, I am aware of projects that were as simple as lightweight bathrooms pods built less than a mile from the project site, to very heavy fully furnished apartment modules that were shipped hundreds of miles, over both seas and roads, and even between two countries. The cost of the transportation was clearly very different being much greater in the second example, yet both projects made financial sense.
To understand the impacts of transportation, keep in mind that costs associated with transportation are not new or exclusive to prefab vs site built. All building construction has transportation costs inherent in the project. Regardless of the method of construction, both materials and labor come from somewhere other than the construction site.
To understand the differences, however, let’s first consider the case of the transportation of labor. In this regard, offsite construction is particularly efficient vs onsite. Workers at a factory tend to live near the factory and so have very consistent and minimal travel distances to the work site (ie the factory). Additionally, carpooling and other energy efficient commuting options become very real in this scheme. In the case of onsite construction, the travel distance for labor is a variable and completely dependent on the location of the trades needed and the building being constructed. Onsite construction requires a more skilled labor force than offsite construction. It is often the case the specialty trades will travel greater distances to reach a construction site than unskilled labor to factories. For onsite construction the location of the worker to the work site is in constant flux with each building built. This is not so with offsite methods.
There is a similar effect with the delivery of materials. Offsite construction occurs on singular factory sites where there tends to be large and protected staging areas. This means materials can be ordered and stored in weather protected areas in bulk far in advance of assembly. Factories also tend to be geographically clustered and located within proximities to construction material suppliers. These two factors greatly increase the efficiency of material delivery to the point of assembly.
For prefab, there is then unique cost of transporting large assemblies to the building site. Unlike traditional onsite labor and material logistics, however, prefab assemblies carry with them substantial embodied bulk material and embodied bulk labor, and are thus extremely efficient transportation hauls.
Because of these efficiencies and the addition of labor to the total transportation cost of building, the equation of transportation related costs and its percentage of the total building cost, has many components and modifiers to consider in the final equation. This is why, depending on the project, it can actually be cost effective to ship large and heavy modules long distances.
Related link: http://www.newschoolarch.edu
© Miletus Group, Inc. 2011
Modular Architecture Q&A: Time and Money
James B. Guthrie, AIA, the President of Miletus Group, Inc, was recently approached by Norman Gray, a graduate student at the New School of Architecture and Design in San Diego, CA regarding an architectural project he was working on. As a part of his research, Mr. Gray sought our expertise in answering several questions regarding prefab and modular construction. We thought the questions were very good ones and worth sharing with a wider audience. We will post each question and answer as a separate blog post. Readers who have their own questions about modular architecture are encouraged to ask us as well.
Question:
What percentage of time and money do you think prefab can save a project?
Answer:
When it comes to prefab, generalized questions can be difficult to answer. In general, on a direct apples-to-apples comparison, I would say that you could expect that a prefab project can be 0-15% less per square foot than a traditionally built project of the same design and specifications. There are too many variables, though, to allow a hard and fast rule as to discounts.
It is also important to keep in mind that when we are talking about prefab, we can be talking about prefab architecture or prefab building. When I talk about prefab architecture, I am using the idea that architecture is a high quality building designed by a professional and it is always site specific. This means that each prefab architecture project will be unique to the site it is being placed on. The quality of the end result will be high quality, and the owner will be a ‘client’ of a professional architect. Prefab building, in contrast, is a generic ‘product’ that can be non-site specific. The quality can vary dramatically from project to project and the owner of this product is a customer of a building company.
The other important thing to consider is the definition of “project”. Architects tend to think of a project as the specific building they are working on. Building owners, however, think of a “project” as the entire business model related to that building. This includes the architecture plus: land acquisition and development, operations and maintenance, financing, cash flow and other business considerations. To answer the question about prefab architecture from the architect’s side, at this time a prefab architecture project has no inherent time or money advantages to the architect except as it may add value for their clients. To answer the question from the owner’s perspective regarding prefab architecture, it can have significant time savings, which to the owner can translate into a huge financial savings to the non-architectural aspects of the project. The amount of savings is, of course, dependent on the project.
Typical Modular Home, USA
2 Offsite Stories, 1 Single Family House, 4 Modules
On the small scale, in the US right now it is very easy for a homebuyer to buy a house much like they buy a car. The homebuyer can go to a sales lot of a manufactured home builder, tour model homes, pick out their model, pick out colors and finishes, and have their new home delivered in a very short amount of time. These homebuyers are buying a prefab building, not prefab architecture. The opportunity for this kind of building to become architecture is very limited. Because prefabrication is a method of construction that takes advantage of manufacturing processes, the economic side of prefab is most successful when there is volume on the production side. One single family home does not afford current manufacturing processes the kind of efficiencies needed to be cost effective. In the case of a home or small commercial building, volume is achieved when many of the same design are produced. In this situation, the efficiency is dispersed among many buyers. This means, naturally, that each individual buyer looses the opportunity to influence the design and quality of their purchase.
Modular Housing, England
10 Offsite Stories, 162 Apartments, 630 Modules
On the large scale, the prefab building buyer is also buying the convenience of speed to occupancy, but the larger scale can allow the project to be more architectural. Fundamentally the building process is relatively the same between prefab and onsite construction, except that the offsite components can be built simultaneously with much of the onsite work. The onsite assembly of the offsite components can then occur very rapidly. On a large project this can save a lot of time, and thus a lot of money to the owner. This is important, as even if the square footage costs of onsite and offsite construction are nearly identical, the cost savings to the owner can be very significant and far exceed the 0-15% savings in square footage costs. Unlike a single family home, the size of a large project can allow the design to take on far more significant role than is possible in small projects. It is the large projects that create the greatest opportunity for all the benefits of prefabrication and the application of real architecture to meld. This is the future of prefabrication in architecture.
Related link: http://www.newschoolarch.edu
© Miletus Group, Inc. 2011
Is Modular Design Really Greener? Exploring Construction Waste Reduction.
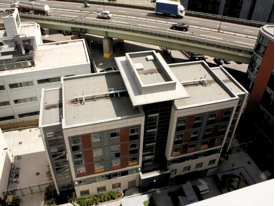
© James B Guthrie, AIA 2011
Yes, there is no question that modular construction is greener. Take the example of construction waste – off-site methods are far more efficient in terms of construction waste reduction than on-site construction.
Here is one example; many on-site contractors will include up to a 10% material contingency in their projects to cover, among other things, damage from weather and trades damages during construction. Because on-site contractors do not normally store excess materials for future jobs, even if there were no damages, this 10% contingency winds up in the waste stream.
Off-site factories are naturally more efficient with their materials. At Miletus Group we own our own modular factory. When we calculate materials for a job we use a factor of 0% percent for weather and trades damages to materials. This makes our overall waste stream very small. Because our facility is organized and weather tight, it is very easy for us to handle materials and waste. Throughout our facility we have separate bins for various construction materials that we can not use again. This means recycling is easy for us and we wind up recycling over 95% of the limited waste we do generate. Very little of our construction material winds up in the landfill. It would be great if on-site builders could make similar claims, but it is highly improbable that on-site construction could ever meet these numbers due to the very nature of the environment in which they work.
Visit AIA’s new KnowledgeNet Modular and Prefabricated Architecture group. There are a couple of documents from the UK on this very subject. They are a few years ahead of us on this issue. It is good reading.
If anyone reading this has further data to support the efficiencies of off-site construction, please do feel free to let us know directly and we will post it.
© Miletus Group, Inc. 2011