Zero Net Energy Classroom at Modular Architecture Group
Zero Net Energy Classroom at Modular Architecture Brown Bag Group meeting Jan 31, 2012 in San Diego
The discussion will include American Modular Systems’ CHPS verified and award winning zero net energy Gen7 modular classroom.
January’s guest will be Jim Wallace of AMS. AMS is a California manufacturer of commercial, institutional, and modular buildings.
All AIA members are welcome to join the meeting.
Brown Bag Roundtable: Modular Architecture
Tuesday, January 31, 2012 — 12:00 – 1:30PM
AIA San Diego Chapter Office
© Miletus Group, Inc. 2012
Modular Architecture Q&A: Project Size vs Economics
Below is the next post, number 3, in the continuing series of prefab/modular Q&A asked by Norman Gray, a graduate student at the New School of Architecture and Design in San Diego, CA and answered by James B. Guthrie, AIA, President of Miletus Group, Inc.
Question:
Is there a minimum size for a project to make prefab economically viable?
Answer:
No. Prefab is a generic concept that has been used to make buildings as small as garden sheds (1 small module) and as large as a 24 story apartment building (500+ large modules). Viability is determined by all the factors that go into making the building, including understanding the supply chain that produces the factory made components and the efficiencies inherent in that chain.
In the case of the garden shed, the sheds are standard designs produced by the hundreds, if not thousands. In the case of the 24 story building, the resulting building is a single architectural structure. One commonality that lead to the economic success in both examples is the use of repetition where repetition made sense. In the case of the garden shed, repetition is probably obvious as each shed is a copy of a singular design. In the example of the 25 story building, the architect cleverly exploited repetition in the layout of the apartments so that very few unique modules were used yet an overall creative architectural solution was achieved.
The fundamental lesson of economic viability here is that if you want to use prefab for a small building, make many replicas of the same building. If you want to use prefab for a large building, make it from many similar components.
Related link: http://www.newschoolarch.edu
© Miletus Group, Inc. 2011
Miletus Group’s green modular solutions featured in Building Indiana News
Miletus Group’s HPMO and Jobsite Leasing’s Green Fleet was featured in Building Indiana News in an article about new mobile and modular solutions. Click on the image below to read the article online – page 58. According to Building Indiana, “Miletus Group and Jobsite Leasing Company have created the mobile office industry’s first green options.” For more on the project, link to our previous blog story here.
Is Modular Design Really Greener? Exploring Construction Waste Reduction.
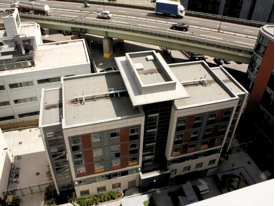
© James B Guthrie, AIA 2011
Yes, there is no question that modular construction is greener. Take the example of construction waste – off-site methods are far more efficient in terms of construction waste reduction than on-site construction.
Here is one example; many on-site contractors will include up to a 10% material contingency in their projects to cover, among other things, damage from weather and trades damages during construction. Because on-site contractors do not normally store excess materials for future jobs, even if there were no damages, this 10% contingency winds up in the waste stream.
Off-site factories are naturally more efficient with their materials. At Miletus Group we own our own modular factory. When we calculate materials for a job we use a factor of 0% percent for weather and trades damages to materials. This makes our overall waste stream very small. Because our facility is organized and weather tight, it is very easy for us to handle materials and waste. Throughout our facility we have separate bins for various construction materials that we can not use again. This means recycling is easy for us and we wind up recycling over 95% of the limited waste we do generate. Very little of our construction material winds up in the landfill. It would be great if on-site builders could make similar claims, but it is highly improbable that on-site construction could ever meet these numbers due to the very nature of the environment in which they work.
Visit AIA’s new KnowledgeNet Modular and Prefabricated Architecture group. There are a couple of documents from the UK on this very subject. They are a few years ahead of us on this issue. It is good reading.
If anyone reading this has further data to support the efficiencies of off-site construction, please do feel free to let us know directly and we will post it.
© Miletus Group, Inc. 2011